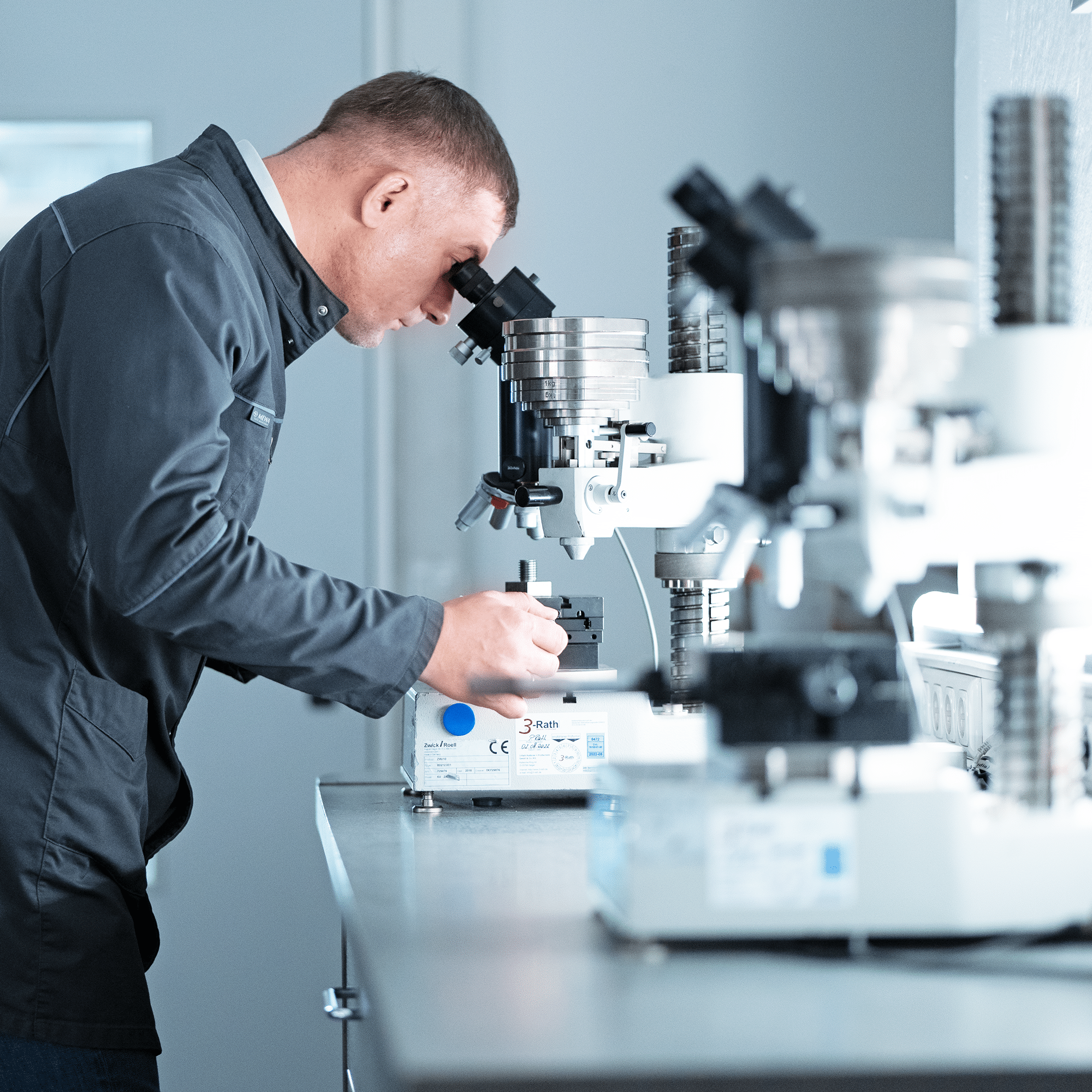
What is the hardness test?
The hardness test is a depth difference method that measures the resistance of the material to permanent deformation. For this purpose, a penetrator is pressed onto the material with a specific test force. The resulting penetration depth or the permanent impression in the test specimen is then measured, and the hardness value of the metal is calculated.
The different types of hardness tests are distinguished, on the one hand, by the shape and material of the penetrator. This body is usually made of steel, carbide, or diamond, and generally possesses a pyramidal, conical, or spherical shape. In addition, other distinguishing characteristics are the size and type of the load. The tests are furthermore categorised into static tests with a constant load, and dynamic tests with an impact load.
What hardness testing methods are there?
The most widely used methods are the standardised static hardness tests as per Rockwell, Vickers, and Brinell. The use of these standard methods produces values that are internationally consistent and comparable.
Rockwell hardness test
The Rockwell test provides a fast method for testing the hardness of metals, and produces values that can be read directly. While primarily suitable as a rapid test and for large material samples, this method is also used for more thorough tests such as the Jominy end-quench test.
In the Rockwell hardness test, a diamond cone is pressed into the material as a penetrator – initially with a preliminary force to avoid errors due to unclean surfaces, and then with the testing force. The resulting penetration depth determines the Rockwell hardness.
The measurement units HR and HRC are commonly used. HR stands for Hardness/Hardness Rockwell, while C stands for Cone – in addition to indicating the procedure, HRC thus also specifies the test head and the hardness scale.
Vickers hardness test
Generally suitable for all solid materials, the Vickers hardness test is also used in the metal industry, for example to control the quality of welds and edge layers. It can be used in both the macro and the micro range if the surface is ground flat.
During a Vickers hardness test, a symmetrical diamond pyramid is used as a test head which, under the application of the test force, leaves an impression in the material under application of the test force.
The diagonals of this impression are measured optically and are used to determine the Vickers hardness (HV).
Knoop hardness test
The Knoop hardness test is used mainly for brittle materials such as ceramics, and for coatings. An asymmetric pyramidal diamond serves as the test head, and presses down on the material with a slight force to prevent cracking, allowing penetration into thin layers. The Knoop hardness (HK) is derived from the optical measurement of the long diagonals.
Brinell hardness test
The oldest common method for hardness testing is the Brinell test. It was developed by Johan August Brinell as early as 1900. The Brinell hardness test is suitable for materials with an inhomogeneous or coarse particle size distribution, and for large samples, because this test method creates a rather large impression. A ball made of tungsten carbide is used as the penetrator. Accordingly, the acronym HBW (Hardness Brinell Tungsten Carbide Ball Indenter) is used as the measurement unit.
When is each test method used?
Which of the four methods for hardness testing is used depends primarily on the type of material, hardness, and treatments of the workpiece. Other factors are the homogeneity of the structure and the size of the component.
It is important that the section of the material to be tested is representative of the entire workpiece. If the microstructure is particularly heterogeneous, the test area must be correspondingly large.
The choice of hardness testing can furthermore depend on standards as well as the number of samples and the required accuracy of the test result.
What is measured during the hardness test?
The result for the hardness derives from different parameters that vary with the selected hardness test. In addition to the distinction between static and dynamic hardness testing, the static methods are further divided into depth measurement methods and optical measurement methods.
Dynamic hardness testing
During dynamic hardness tests, the force exerted by the test head is applied abruptly. The Leeb rebound method (ISO 16589), for example, is performed by shooting a sphere at the material to be tested, and then measuring the height of the rebound.
Another example is the UCI method (DIN 50159-1), which is short for Ultrasonic Contact Impedance. This method measures the resonance displacement of an ultrasonic vibration rod, which results from the contact of the test head with the material surface.
Depth measurement methods
The Rockwell method (HR) is a depth measurement method standardised as per ISO 6508. Brinell (HBT) and Vickers (HVT) can also be measured by depth. However, these procedures are not standardised. It is common to all procedures that they measure the test head's depth of penetration.
Optical measurement methods
Brinell (ISO 6506), Knoop (ISO 4545) and Vickers (ISO 6507) take measurements using optical measurement methods based on norms and standards. These methods measure the impression size that the test head leaves behind in the material. This measurement is followed by the calculation of the hardness based on a formula.
The test force applied in the hardness test
The test force applied during the hardness test is defined as the force with which the penetrator acts on the material to be tested. The greater the impression remaining in the material, the greater the accuracy of the measurement. For testing, it is therefore advisable to always use the maximum permissible test force.
Test forces are officially specified in Newton (N), but are often measured internally in gramme force (gf), kilogramme force (kgf) or pond (p). 1 kgf equals 1,000 p or 9.81
N. Above and below 1 kgf the hardness test is classified as a macrohardness test, and below this value it is a microhardness test.
Accuracy and reproducibility
Only proper procedure ensures the accuracy and reproducibility of hardness tests. As a general rule, if the test force is low then an exact result usually requires consideration of more parameters. The following factors must be taken into account:
- A controlled environment (temperature, humidity, vibrations, etc.)
- Calibration of the test device
- No impurities on the material or test device
- The test device and the test head respectively must be aligned horizontal and perpendicular to the material surface
- The material sample must be fixed stably in place
- Constant lighting conditions are important for optical measurement methods
Surface preparation for the hardness test
In many cases, the execution of a hardness test requires the surface to be prepared accordingly. This preparation can involve chemical, electrochemical, or mechanical processes. It is important that the properties of the material surface to be tested remain unchanged.
The quality of the surface preparation has a direct effect on the accuracy of the test result. Which method is suitable depends on the condition of the material surface and on the type of hardness test, the penetrator used, and the test force.
Preparation is not necessarily required for a macrohardness test (test force above 1 kgf). Fine grinding will suffice in most cases. In contrast, the surface to be subjected to a microhardness test (test force below 1 kgf) must be polished mechanically or by means of electrolysis. The objective is a clearly visible edge for the optical measurement of the impression.
Deformations during preparation
Deformations can occur during sampling and must be polished – with an accuracy of 6.3 μm to 1 μm, depending on the planned test force. The lower the test force, the lower the number of permissible deformations. Below 300 gf, the surface must be free of deformations or damage.
Depending on the planned hardness test, the following steps may be necessary for surface preparation:
Hardness testing method | Surface preparation |
Rockwell (macrohardness test) | No surface preparation, grinding |
Brinell (macrohardness test) | Grinding, polishing or lapping |
Vickers (macrohardness test) | Grinding |
Vickers (microhardness test) | Mechanical, polishing electropolishing |
Knoop (microhardness test) | High-gloss polishing, electropolishing |
Areas of application for hardness tests
The hardness test plays a major role in the quality assurance applied by various industries, as it can often be carried out in a nearly non-destructive manner.
The metal industry in particular commonly relies on this testing method , for example as a means to examine welds or verify the success of heat treatments and surface finishes. In addition, the hardness test is also of relevance in the area of positive material identification (PMI).
Process locations
At Härtha, we use hardness tests for quality assurance at all locations. Refer to our interactive location overview to also learn the metal processing processes which we offer at locations near you.