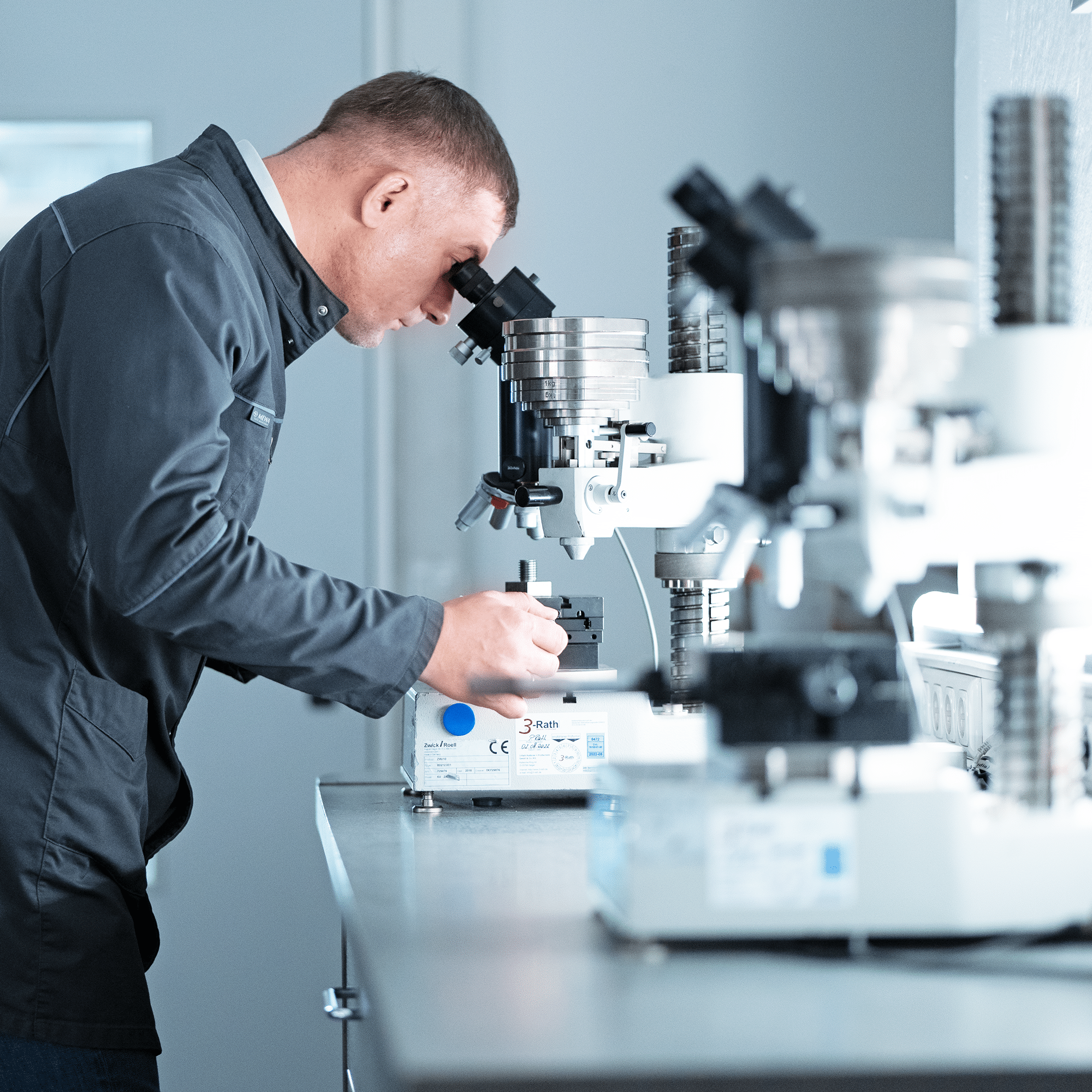
Cos’è la prova di durezza?
La prova di durezza è un metodo che misura la differenza di profondità di penetrazione, durante il quale la resistenza del materiale viene misurata in base a una deformazione permanente. Per eseguire la prova, un penetratore viene spinto nel materiale con una determinata forza di prova. Successivamente viene misurata la profondità di penetrazione creatasi ovvero l’impronta permanente nel provino e viene calcolato il valore di durezza del metallo.
I diversi tipi di prova di durezza si distinguono, da un lato, per la forma e, dall’altro, per il materiale del penetratore. Quest’ultimo è solitamente realizzato in acciaio, carburo di tungsteno o diamante e ha forma piramidale, conica o sferica. Inoltre si distinguono per entità e tipo di carico: vi sono le prove statiche, con carico costante e quelle dinamiche, con carico applicato quale urto.
Quali metodi esistono per la prova di durezza?
I metodi per la prova di durezza più diffusi sono quelli statici normalizzati Rockwell, Vickers e Brinell. L’uso di questi metodi normalizzati consente di ottenere valori di misura uniformi e confrontabili a livello internazionale.
Prova di durezza Rockwell
Il Rockwell è un metodo rapido per la prova di durezza dei metalli, in cui i valori possono essere letti direttamente. È adatto principalmente quale test rapido e per campioni di materiali di grandi dimensioni, ma è usato anche per test più accurati come la prova di temprabilità di Jominy.
Nella prova di durezza Rockwell un cono diamantato viene premuto contro il materiale quale penetratore - inizialmente con una pre-forza di prova, in modo da evitare errori dovuti a superfici non pulite, e successivamente con la forza di prova.
La durezza Rockwell si calcola quindi dalla profondità di penetrazione risultante.
Le unità di misura solita mente usate sono HR e HRC. HR sta per Hardness (durezza) Rockwell e C per Cone (cono) – con HRC vengono quindi indicati, oltre al metodo, anche il penetratore e la scala di durezza.
Prova di durezza Vickers
La prova di durezza Vickers è adatta in generale per tutti i materiali solidi e viene utilizzata anche nell’industria metallurgica, ad esempio per il controllo di giunti saldati e di strati superficiali. Può essere impiegata sia nel range macro che in quello micro, purché la superficie sia levigata in modo da essere piana.
Nella prova di durezza Vickers viene utilizzato un penetratore piramidale diamantato simmetrico che lascia un'impronta nel materiale quando viene applicata la forza di prova.
Le diagonali di tale impronta vengono misurate otticamente e servono a determinare la durezza Vickers (HV).
Prova di durezza Knoop
La prova di durezza Knoop è usata principalmente per materiali fragili, come ceramica e rivestimenti. Si utilizza un penetratore piramidale diamantato asimmetrico, che preme sul materiale con una forza ridotta, in modo da evitare criccature e da rendere possibile la penetrazione in strati sottili. La durezza Knoop (HK) si ricava dalla misura ottica delle diagonali lunghe.
Prova di durezza Brinell
Il più antico metodo usato per la prova di durezza è il Brinell. Fu inventato già nel 1900 da Johan August Brinell. Visto che con questo metodo si crea un'impronta piuttosto grande, la prova di durezza Brinell è adatta per materiali con distribuzione della grana disomogenea o grossolana e per campioni di grandi dimensioni. Come penetratore si usa una sfera in carburo di tungsteno. In questo caso l’unità di misura usata è HBW.
Quando e quale metodo di prova usare?
Quale dei quattro metodi di prova usare dipende soprattutto dal tipo di materiale, dalla durezza, dai trattamenti del pezzo e dall’uniformità della struttura, ma anche dalle dimensioni del componente.
È importante che il ritaglio di materiale da esaminare sia rappresentativo dell’intero pezzo. Se la struttura è molto eterogenea l’area di prova deve avere dimensioni sufficientemente grandi.
Inoltre anche le norme possono influenzare la scelta della prova di durezza, il numero di campioni e la precisione del risultato della prova richiesta.
Cosa si misura nella prova di durezza?
L’indicazione della durezza si basa su diversi parametri che, a loro volta, dipendono dalla prova di durezza. Oltre alla distinzione tra prove di durezza statiche e dinamiche, i metodi statici si suddividono ulteriormente in metodi di misura della profondità e metodi ottici.
Prova di durezza dinamica
Nelle prove di durezza dinamiche la forza è applicata sotto forma di urto. Ad esempio nel metodo a rimbalzo secondo Leeb (ISO 16589) una sfera viene sparata sul materiale da testare e successivamente viene misurata l'altezza del rimbalzo.
Un ulteriore esempio è il metodo UCI (DIN 50159-1), quale acronimo di Ultrasonic Contact Impedance. In questo caso si misura il cambiamento di risonanza di un’asta oscillante a ultrasuoni che si determina al contatto del diamante piramidale montato sull’estremità dell’asta con la superficie del materiale.
Metodo di misura della profondità
Il Rockwell (HR) è un metodo di misura della profondità normalizzato in ISO 6508. Anche Brinell (HBT) e Vickers (HVT) possono essere misurati in base alla profondità. Tuttavia questi procedimenti non sono normalizzati. La caratteristica comune di tutti i metodi è che viene misurata la profondità di penetrazione nel provino.
Metodi di misura ottici
Brinell (ISO 6506), Knoop (ISO 4545) e Vickers (ISO 6507) misurano in maniera standardizzata e normalizzata con l'ausilio di metodi ottici. Sono misurate le dimensioni dell’impronta lasciata nel provino del materiale. La durezza viene quindi calcolata mediante un’apposita formula.
La forza di prova nella prova di durezza
Nell'ambito delle prove di durezza, la forza di prova indica la forza con cui il penetratore agisce sul materiale da testare. Vale la regola per cui quanto più grande è l’impronta che rimane nel materiale, tanto maggiore è la precisione di misura. Per il test si dovrebbe usare quindi sempre la massima forza di prova ammessa.
Le forze di prova sono ufficialmente indicate in Newton (N), internamente spesso e volentieri anche in grammo-forza (gf), chilogrammo-forza (kgf) o pond (p). 1 kgf corrisponde a 1.000 p o 9,81 N. Sopra a 1 kgf si parla di prova di macrodurezza, al di sotto di prova di microdurezza.
Precisione e riproducibilità
Un procedimento corretto è indispensabile per garantire la precisione e riproducibilità delle prove di durezza. In linea di principio vale la regola per cui, per ottenere un risultato esatto, quanto minore è la forza di prova tanti più parametri devono essere rispettati. Vanno tenuti in considerazione i seguenti fattori:
- Ambiente controllato (temperatura, umidità, vibrazioni ecc.)
- Taratura dell'apparecchio di prova
- Assenza di sporco sul materiale o sull’apparecchio di prova
- L’apparecchio di prova deve essere posizionato in orizzontale e il penetratore deve essere orientato verticalmente rispetto alla superficie del materiale
- Il campione di materiale deve essere fissato in modo da risultare stabile
- Per i metodi di misura ottici sono importanti condizioni di luce costanti
Preparazione della superficie nella prova di durezza
Per poter eseguire una prova di durezza, in molti casi è necessario procedere a una preparazione della superficie, che può avvenire con metodi chimici, elettrochimici o meccanici. È importante che le proprietà della superficie del materiale da testare rimangano invariate.
La qualità della preparazione della superficie influenza direttamente la precisione del risultato della prova. Quale sia il processo adatto dipende dalle condizioni della superficie del materiale e dal tipo di prova di durezza, dal penetratore e ancora dalla forza di prova impiegati.
Nella prova di macrodurezza (forza di prova superiore a 1 kgf) non è per forza necessaria una preparazione. In questo caso basta solitamente una levigatura fine. Nella prova di microdurezza (forza di prova inferiore a 1 kgf) la superficie deve invece essere lucidata meccanicamente o mediante elettrolisi. L’obiettivo è quello di ottenere un bordo nettamente visibile per la misurazione ottica dell’impronta.
Deformazioni nella preparazione
Durante il prelievo del campione possono crearsi delle deformazioni che devono essere lucidate – a seconda della forza di prova prevista, con una precisione di 6, 3 µm fino a 1 µm. Quanto più bassa è la forza di prova, tanto minori devono essere le deformazioni. Sotto a 300 gf la superficie deve essere priva di deformazioni o danneggiamenti.
A seconda della prova di durezza prevista per la preparazione della superficie sono necessari i seguenti passaggi:
Metodo di prova della durezza | Preparazione della superficie |
Rockwell (prova di macrodurezza) | Nessuna preparazione, superficiale Levigatura |
Brinell (prova di macrodurezza) | Levigatura, Lucidatura o lappatura |
Vickers (prova di macrodurezza) | Levigatura |
Vickers (prova di microdurezza) | Meccanica, Lucidatura Elettrolucidatura |
Knoop (prova di microdurezza) | Lucidatura a specchio, Elettrolucidatura |
Campi d’impiego delle prove di durezza
La prova di durezza ha un ruolo fondamentale nell’assicurazione qualità in diversi settori, anche perché spesso può essere eseguita in maniera sostanzialmente non distruttiva.
È usata spesso, in particolare nell’industria metallurgica, ad esempio per controllare giunti saldati o per verificare la buona riuscita di trattamenti termici e finiture superficiali. Inoltre la prova di durezza è importante per la prova di identificazione Positive Material Identification (PMI) dei materiali.
Sedi dei processi
In Härtha utilizziamo le prove di durezza per l’assicurazione qualità in tutti gli stabilimenti. La mappa delle sedi indica i processi di lavorazione dei metalli offerti dai vari stabilimenti.