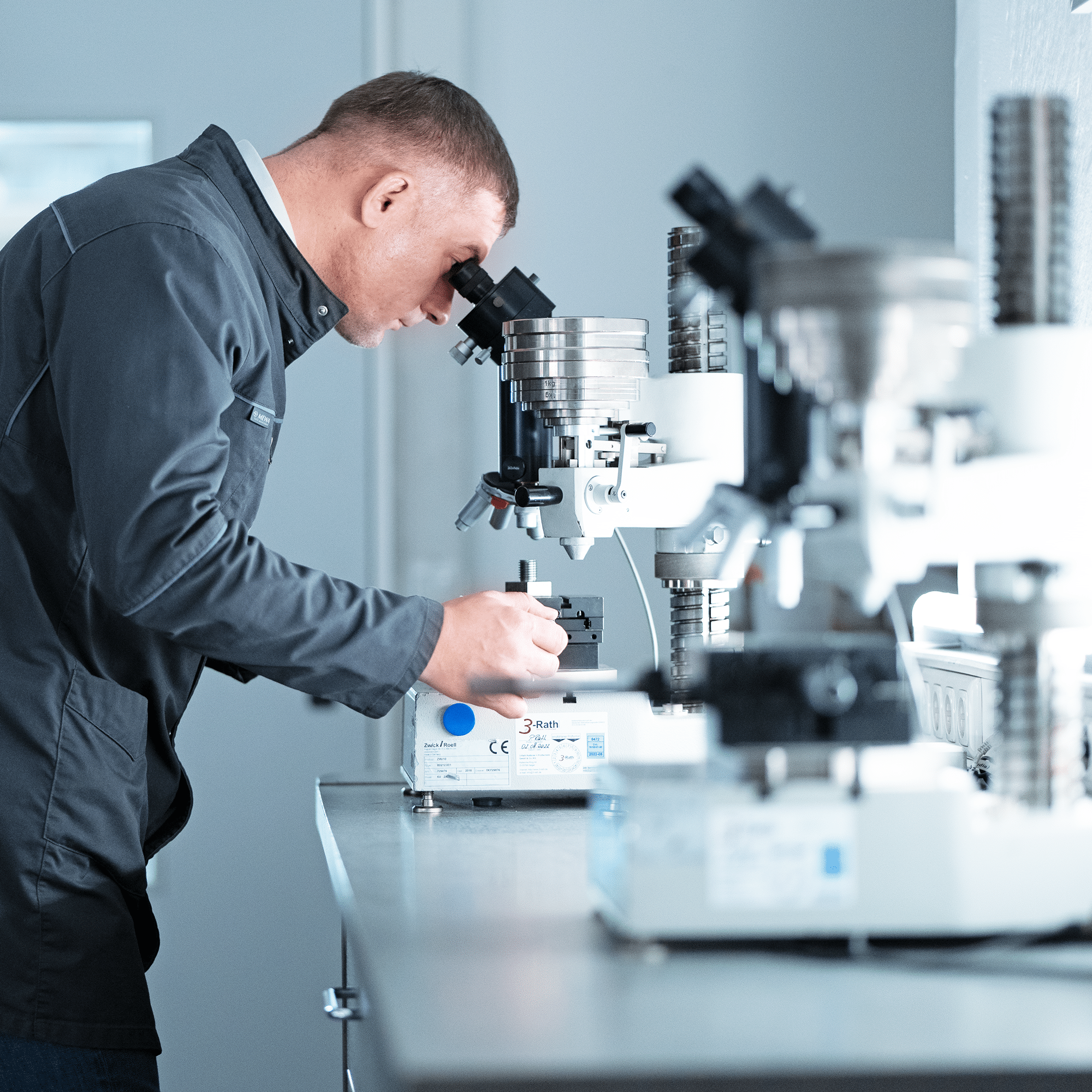
Was ist die Härteprüfung?
Die Härteprüfung ist ein Tiefendifferenzverfahren, bei dem der Widerstand des Werkstoffs gegen eine dauerhafte Verformung gemessen wird. Dazu wird ein Eindringkörper mit einer bestimmten Prüfkraft auf den Werkstoff gedrückt. Anschließend wird die entstandene Eindringtiefe bzw. der bleibende Eindruck des Prüfkörpers gemessen und der Härtewert des Metalls berechnet.
Die unterschiedlichen Arten der Härteprüfung unterschieden sich zum einen nach der Form und dem Material des Eindringkörpers. Dieser ist in der Regel aus Stahl, Hartmetall oder Diamant und pyramiden-, kegel- oder kugelförmig. Zudem wird nach Größe und der Art der Belastung unterschieden. Es gibt die statische Prüfung mit gleichbleibender Belastung und die dynamische Prüfung mit schlagartiger Belastung.
Welche Härteprüfverfahren gibt es?
Am weitesten verbreitet sind die genormten Härteprüfverfahren gemäß Rockwell, Vickers und Brinell. Die Verwendung dieser Normverfahren ermöglicht international einheitliche und vergleichbare Messwerte.
Härteprüfung nach Rockwell
Rockwell bietet ein schnelles Verfahren zur Härteprüfung von Metallen, bei dem die Werte direkt ablesbar sind. Es eignet sich in erster Linie als Schnelltest und für große Werkstoffproben, aber wird auch für gründlichere Prüfungen wie den Stirnabschreckversuch nach Jominy genutzt.
Bei der Härteprüfung nach Rockwell wird ein Diamantkegel als Eindringkörper in den Werkstoff gedrückt – zunächst mit einer Vorkraft, um Fehler wegen unsauberer Oberflächen zu vermeiden, und dann mit der Prüfkraft. Aus der daraus resultierenden Eindringtiefe ergibt sich die Rockwell-Härte.
Die Maßeinheiten HR und HRC sind gebräuchlich. HR steht für Hardness/Härte Rockwell und C für Cone – mit HRC werden neben dem Verfahren also auch der Prüfkörper und die Härteskala angegeben.
Härteprüfung nach Vickers
Die Vickers Härteprüfung eignet sich grundsätzlich für alle festen Werkstoffe und findet ebenfalls in der Metallindustrie ihre Verwendung, zum Beispiel zur Kontrolle von Schweißnähten und Randschichten. Sie kann sowohl im Makro- als auch im Mikrobereich eingesetzt werden, wenn die Oberfläche plan geschliffen ist.
Bei der Härteprüfung nach Vickers wird eine symmetrische Diamantpyramide als Prüfkörper verwendet, die unter Aufwendung der Prüfkraft einen Eindruck im Werkstoff hinterlässt. Die Diagonalen dieses Eindrucks werden optisch vermessen und dienen zur Ermittlung der Vickers-Härte (HV).
Härteprüfung nach Knoop
Die Härteprüfung nach Knoop wird vor allem bei spröden Werkstoffen wie Keramik und für Beschichtungen eingesetzt. Ein asymmetrischer pyramidenförmiger Diamant dient als Prüfkörper, der mit wenig Kraft auf den Werkstoff drückt, um Rissbildung zu vermeiden und das Eindringen in dünne Schichten zu ermöglichen. Die Knoop-Härte (HK) ergibt sich aus der optischen Vermessung der langen Diagonalen.
Härteprüfung nach Brinell
Die älteste gebräuchliche Methode zur Härteprüfung ist das Brinell-Verfahren. Es wurde bereits 1900 von Johan August Brinell entwickelt. Die Härteprüfung nach Brinell eignet sich für Werkstoffe mit inhomogener oder grober Kornverteilung und für große Proben, da bei diesem Prüfverfahren ein eher größerer Eindruck entsteht. Als Eindringkörper wird eine Kugel aus Wolframkarbid genutzt. Entsprechend wird die Maßeinheit HBW (Härte Brinell Wolframkarbidkugel) abgekürzt.
Wann wird welches Prüfverfahren genutzt?
Welche der vier Methoden zur Härteprüfung eingesetzt wird, hängt vor allem von der Werkstoffsorte, der Härte und den Behandlungen des Werkstücks ab sowie von der Homogenität des Gefüges, aber auch von der Größe des Bauteils.
Wichtig ist, dass der zu prüfende Materialausschnitt repräsentativ für das gesamte Werkstück ist. Bei einem sehr heterogenen Gefüge muss der Prüfbereich entsprechend groß ausfallen.
Zudem können Normen einen Einfluss auf die Wahl der Härteprüfung haben sowie die Anzahl der Proben und die notwendige Genauigkeit des Prüfergebnisses.
Was wird bei der Härteprüfung gemessen?
Je nach Härteprüfung ergibt sich die Angabe der Härte aus unterschiedlichen Parametern. Neben der Unterscheidung nach statischer und dynamischer Härteprüfung, unterteilt man die statischen Verfahren zusätzlich in Tiefenmessverfahren und optische Messverfahren.
Dynamische Härteprüfung
Bei dynamischen Härteprüfungen wird die Krafteinwirkung des Prüfkörpers schlagartig ausgeführt. Bei der Leeb-Rückprallmethode (ISO 16589) wird beispielsweise eine Kugel auf das zu prüfende Material geschossen und anschließend die Höhe des Rückpralls gemessen.
Ein weiteres Beispiel ist das UCI-Verfahren (DIN 50159-1), kurz für Ultrasonic Contact Impedance. Hierbei wird die Resonanzverschiebung eines Ultraschallschwingstabs gemessen, die sich beim Kontakt des Prüfkörpers mit der Materialoberfläche ergibt.
Tiefenmessverfahren
Das Rockwell-Verfahren (HR) ist ein nach ISO 6508 genormtes Tiefenmessverfahren. Auch Brinell (HBT) und Vickers (HVT) können nach Tiefe gemessen werden. Diese Verfahren sind aber nicht genormt. Allen Verfahren ist gemein, dass die Eindringtiefe des Prüfkörpers gemessen wird.
Optische Messverfahren
Brinell (ISO 6506), Knoop (ISO 4545) und Vickers (ISO 6507) messen standardisiert und genormt mittels optischen Messverfahrens. Dabei wird die Eindrucksgröße gemessen, die der Prüfkörper im Material hinterlässt. Mithilfe einer Formel wird dann die Härte berechnet.
Die Prüfkraft bei der Härteprüfung
Die Prüfkraft beschreibt bei der Härteprüfung die Kraft, mit welcher der Eindringkörper auf das zu prüfende Material einwirkt. Dabei gilt, je größer der verbleibende Eindruck im Material, desto höher die Messgenauigkeit. Zum Prüfen sollte also immer die höchstzulässige Prüfkraft verwendet werden.
Prüfkräfte werden offiziell in Newton (N) angegeben, intern aber gerne in Gramm-Force (gf), Kilogramm-Force (kgf) oder Pond (p) gemessen. 1 kgf entspricht dabei 1.000 p bzw. 9,81 N. Oberhalb von 1 kgf spricht man von der Makrohärteprüfung, darunter von der Mikrohärteprüfung.
Genauigkeit und Reproduzierbarkeit
Nur eine ordnungsgemäße Vorgehensweise gewährleistet die Genauigkeit und Reproduzierbarkeit von Härteprüfungen. Grundsätzlich gilt, dass bei geringerer Prüfkraft in der Regel mehr Parameter für ein exaktes Ergebnis beachtet werden müssen. Folgende Faktoren sind zu berücksichtigen:
- Eine kontrollierte Umgebung (Temperatur, Feuchtigkeit, Vibrationen etc.)
- Kalibrierung des Prüfgeräts
- Keine Verschmutzungen auf dem Material oder Prüfgerät
- Das Prüfgerät muss horizontal und der Prüfkörper senkrecht zur Materialoberfläche ausgerichtet sein
- Die Materialprobe muss stabil fixiert sein
- Bei optischen Messverfahren sind konstante Lichtverhältnisse wichtig
Die Oberflächenpräparation bei der Härteprüfung
Um eine Härteprüfung vornehmen zu können, muss in vielen Fällen eine Oberflächenpräparation erfolgen. Das kann durch chemische, elektrochemische oder mechanische Verfahren erfolgen. Wichtig ist, dass die Eigenschaften der zu prüfenden Materialoberfläche unverändert bleiben.
Die Qualität der Oberflächenpräparation hat direkten Einfluss auf die Genauigkeit des Prüfergebnisses. Welches Verfahren sich eignet, ist abhängig vom Zustand der Materialoberfläche und von der Art der Härteprüfung bzw. vom genutzten Eindringkörper und der Prüfkraft.
Bei der Makrohärteprüfung (Prüfkraft über 1 kgf) muss nicht zwingend eine Präparation vorgenommen werden. Hier reicht meist ein Feinschliff. Bei einer Mikrohärteprüfung (Prüfkraft unter 1 kgf) muss die Oberfläche hingegen mechanisch oder mittels Elektrolyse poliert werden. Ziel ist eine deutlich sichtbare Kante zur optischen Vermessung des Eindrucks.
Verformungen bei der Präparation
Bei der Probenentnahme können Verformungen entstehen, die poliert werden müssen – je nach geplanter Prüfkraft mit einer Genauigkeit von 6, 3 μm bis 1 μm. Je geringer die Prüfkraft, desto weniger Verformungen dürfen vorliegen. Unter 300 gf muss die Oberfläche frei von Verformungen oder Schädigungen sein.
Je nach geplanter Härteprüfung sind folgende Schritte zur Oberflächenvorbereitung notwendig:
Härteprüfverfahren | Oberflächenvorbereitung |
Rockwell (Makrohärteprüfung) | Keine Oberflächenpräparation, Schleifen |
Brinell (Makrohärteprüfung) | Schleifen, Polieren oder Läppen |
Vickers (Makrohärteprüfung) | Schleifen |
Vickers (Mikrohärteprüfung) | Mechanisch Polieren, Elektropolieren |
Knoop (Mikrohärteprüfung) | Hochglanzpolieren, Elektropolieren |
Anwendungsbereiche von Härteprüfungen
Die Härteprüfung spielt eine große Rolle in der Qualitätssicherung verschiedenster Branchen, da sie oft nahezu zerstörungsfrei vorgenommen werden kann.
Besonders in der Metallindustrie wird sie häufig eingesetzt, um beispielsweise Schweißnähte zu kontrollieren oder den Erfolg von Wärmebehandlungen und Oberflächenveredelungen zu prüfen. Zudem spielt die Härteprüfung bei der Verwechslungsprüfung (PMI) von Werkstoffen eine Rolle.
Verfahrensstandorte
Härteprüfungen setzen wir bei Härtha an allen Standorten zur Qualitätssicherung ein. In unserer Standortübersicht erfahren Sie außerdem, welche Verfahren zur Metallverarbeitung wir in Ihrer Nähe anbieten.