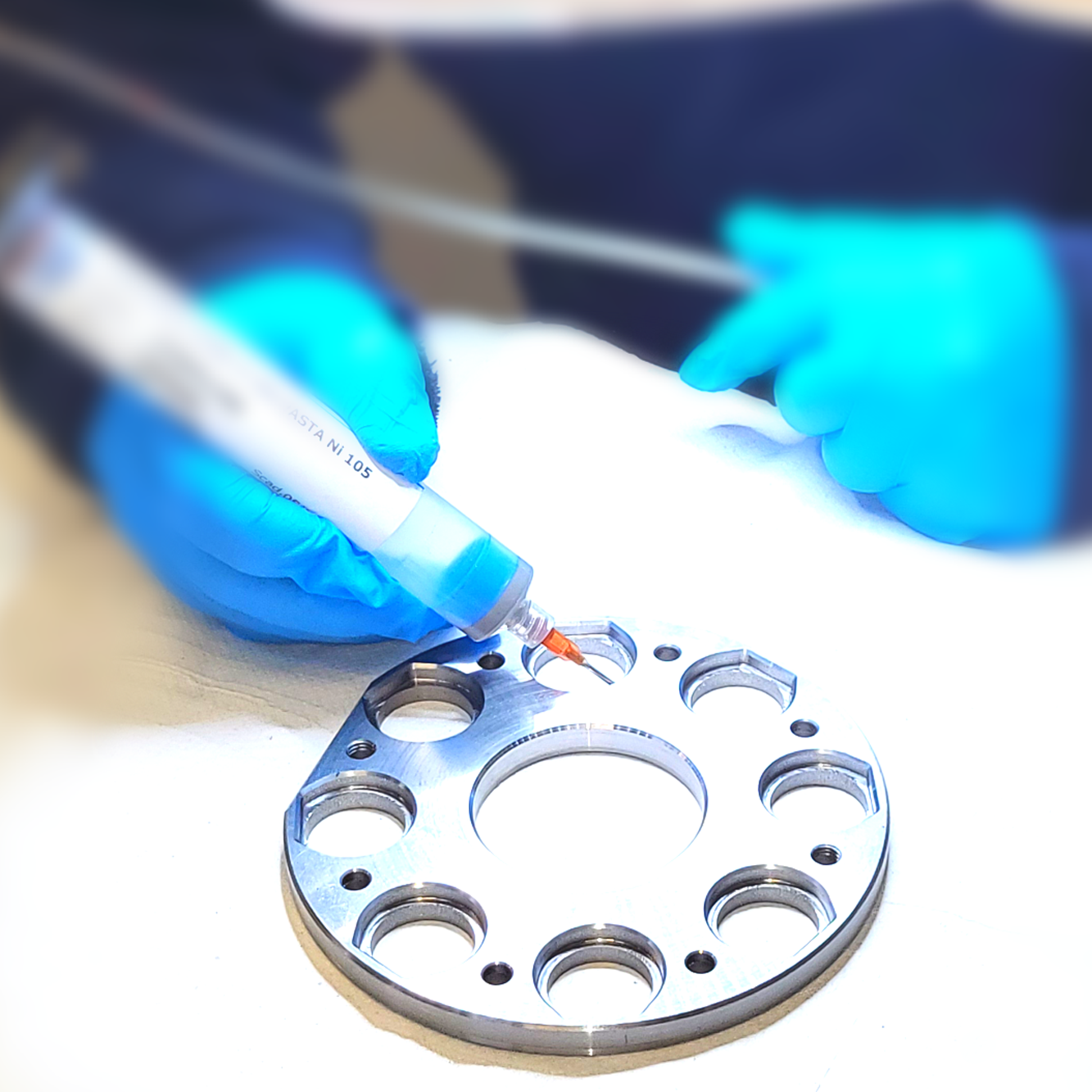
Process and background information
Vacuum brazing is a special hard brazing process based on capillary action. For this, a suitable brazing material is melted and applied as a coating on the parts to be joined. The subsequent cooling creates a firmly bonded joint. The vacuum atmosphere prevents unwanted reactions with the environment, such as oxidation, and provides optimum brazing conditions.
The process starts with a thorough cleaning of the components, in order to remove grease, oxides, and other impurities. Next, the brazing material is applied in the form of a foil, wire, paste, or a galvanic coating. The components are then precisely fixed in place in the vacuum furnace in order to ensure exact positioning.
Once the target temperature has been reached, the brazing material is kept molten for a defined dwell time, ensuring the complete coating of the join surfaces. The controlled cooling keeps the material from warping and ensures a uniform microstructure. To ensure the highest quality standards, the process concludes with a check of the workpieces for strength, tightness, and dimensional accuracy.
Advantages of vacuum brazing
The process offers numerous advantages, including high-strength and reproducible joints with flawless, corrosion-resistant surfaces. Since it does not require fluxes, the process does not produce any residues, thus eliminating the need for costly rework. Another benefit is the option to combine brazing and hardening in a single process step - thus providing an efficient solution that saves time and money.
The key advantages at a glance:
- High strength and corrosion resistance of the joint
- Clean surfaces free of oxides, as no flux residues are produced
- Combination of different materials, e. g. metal/ceramic combinations
- Even heat distribution thanks to the vacuum, minimising dimensional deviations
- Reduced need for rework, as the process does not create any oxidation layers
- Ideal for high-precision applications in the fields of aerospace and medical engineering
Applications and suitable materials
Its versatility has made vacuum brazing an established solution in numerous branches of industry. It very suitable for high alloy steels, super alloys, stainless steel, copper, titanium, and aluminium, as well as for demanding materials such as ceramics, carbides, CBN, and diamond. This compatibility across a wide range of materials makes the process particularly attractive for machine and tool making, where it is used, for instance, for joining carbide and steel.
The process also plays an essential role in aerospace, as it allows the production of extremely strong and temperature-resistant structural components. Its applications in the automotive industry include the production of hydraulic and cooling systems. Medical engineering benefits from the hygienic, gap-free joints that vacuum brazing makes possible, while it is used in vacuum and measurement technology for the production of high-precision components. Another important area of application is the manufacture of heat exchangers and heating elements, which require optimum heat transfer.
Process optimisation and special processes
To achieve even better results, vacuum brazing can be further optimised with the help of a variety of special processes. One common method is vacuum hardening with subsequent tempering, which substantially increases the mechanical strength of the components. Similarly, surface hardening by nitriding contributes to boosting wear resistance, thus improving the durability of the components.
Another key aspect is stress-free annealing, which reduces internal stresses in the material and thus minimises the risk of warping or cracks. Moreover, the targeted use of capillary action can help achieve an even more precise coating of the joining surfaces, and this optimises the quality of the solder joint even further. These specialised processes make it possible to systematically adapt vacuum brazing to specific requirements and thus to ensure even higher performance and reliability.
Would you like to learn more about vacuum brazing? Contact our team of experts!
Process locations
Our locations in Germany and Europe are shown here.