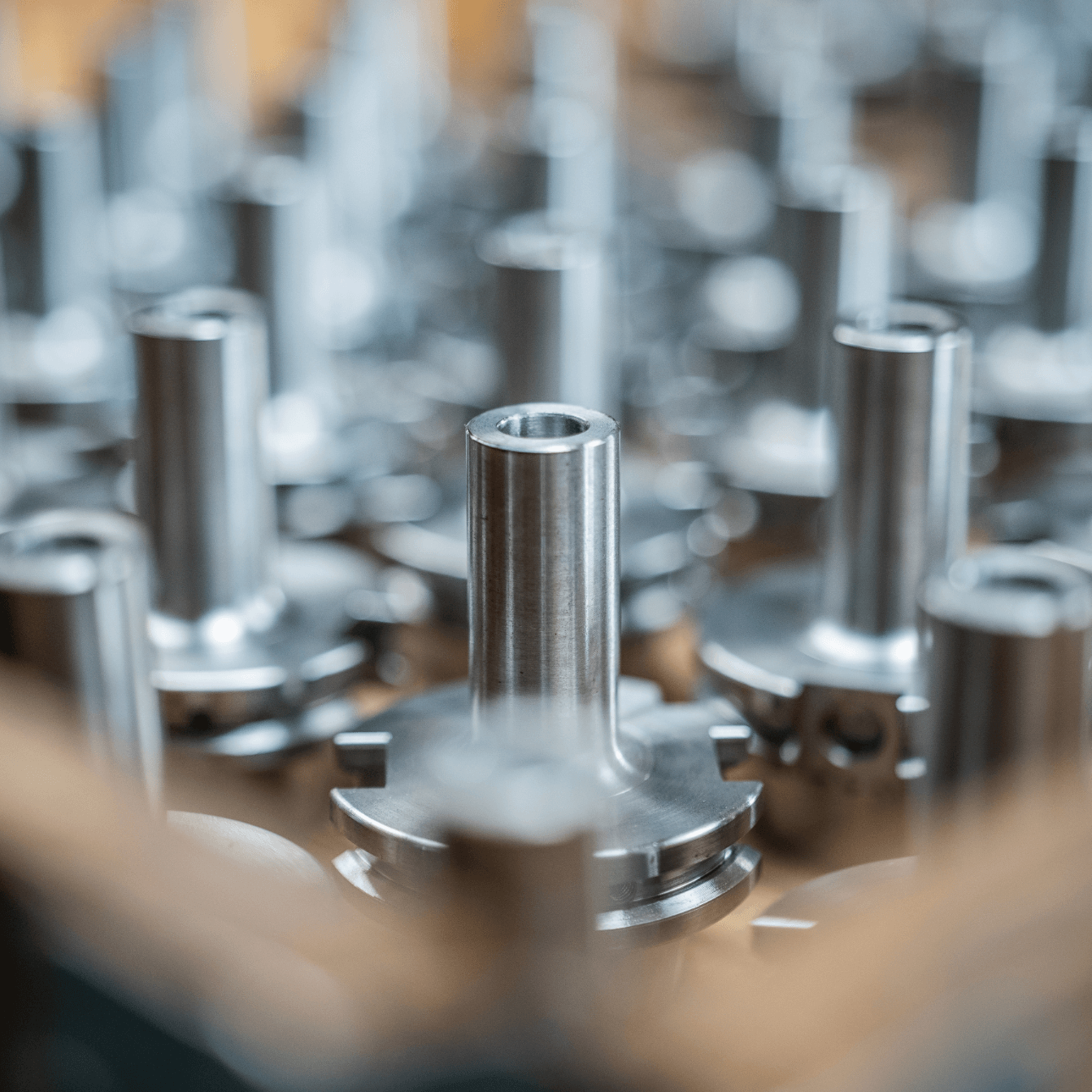
The process: How does electroless nickel plating work?
Electroless nickel plating is a dimensionally stable coating method for nearly all types of metal. A chemical process not requiring an external current deposits the electroless nickel layer at a temperature of approx. 90 °C. The result is an even distribution of the layer thickness across the entire workpiece.
Because electroless nickel plating is exceedingly time-consuming, the process is very expensive. It takes about one hour to produce a thickness of 10 µm. Consequently, thicker layers exceeding 50 µm are rare in practice.
INFO: Difference from galvanic nickel plating
Electrons are necessary to separate nickel ions from the metal. During galvanic nickel plating, an electric current is supplied from an external source such as a rectifier. In contrast, electroless nickel plating produces the necessary electrons itself through a redox reaction that takes place in the bath. This allows contour-accurate coatings with a tolerance between ± 2 μm and ± 3 μm at a coating thickness of 8 μm to 80 μm. However, stresses may form in the electroless nickel coating at thicknesses of 50 µm or more.
Properties of the coating
The properties of the nickel-phosphorus coating can be specifically controlled via the phosphorus concentration. Concentrations of 3% to 7% are classified as a low phosphorus content, 6% to 9% signify a medium phosphorus content, and 10% to 12% indicate a high phosphorus content.
- The higher the phosphorus content, the greater the protection against corrosion. It is furthermore important that the coating is free of pores. This depends on the type of material and the pre-processing of the workpiece (milling, polishing, etc.), as they affect adhesive strength. The corrosion protection layer is usually at least 30 μm to 50 μm thick.
- The lower the phosphorus content, the greater the increase in hardness or wear resistance. An additional heat treatment (up to one hour at a maximum of 400 °C) can produce a hardness level of 800 to 1,100 HV. Common coating thicknesses range between 10 µm and 50 µm.
The appearance of the electroless nickel coating can be altered only to a limited degree, for example by means of brighteners in the electrolyte. Adjustable properties such as the density of the grain boundary can affect the appearance only slightly. The appearance thus largely depends on the pre-processing of the workpiece – shiny surfaces remain shiny, matt surfaces remain matt.
The adhesion strength is also dependent on the type of material and on previous treatments. Heat treatment at low temperatures and a long holding time improve adhesion strength.
Types of processes
Mid-phos electroless nickel plating
(medium phosphorus content)
Mid-phos electroless nickel plating produces a medium phosphorus content (6% to 9%). It is used to increase the hardness (approx. 600 HV) and wear resistance of workpieces and to achieve good corrosion protection (over 480 hours at s/min = 0.030 mm). The workpieces become ferromagnetic. A heat treatment can increase hardness to approx 1,000 HV.
High-phos electroless nickel plating
(high phosphorus content)
High-phos electroless nickel plating produces a high phosphorus content (10% to 12%). This process is ideal for workpieces that are intended to possess very high corrosion resistance (over 500 hours at s/min = 0.030 mm) and must not be magnetic.
Wear resistance and hardness (approx. 550 HV) are lower compared to the mid-phos process. Here too a thermal post-treatment can lead to greater hardness (approx. 900 HV).
Thermal treatment
A thermal post-treatment of electroless nickel-plated workpieces is primarily used to increase the hardness as far as 1,000 (± 50) HV; and also to improve wear resistance and coating adhesion. For this purpose, the workpieces are tempered at 230
°C to 400 °C.
Hybrid coating
Hybrid coating combines all the advantages of the electroless nickel and hard chrome plating processes . Electroless nickel plating is followed by hard chrome plating. This procedure creates a coating system that offers excellent corrosion protection and very high wear resistance. The actual coating thickness depends on the purpose of the application.
Workpieces with a hybrid coating are suitable for use in harsh environments marked by high chemical and mechanical loads.
Barrel coating
During a barrel coating procedure, the workpieces are placed in a perforated barrel that rotates around its own axis. The rotation ensures that all workpieces are treated in the same way. This process is used for bulk goods such as screw connectors.
Rack coating
Electroless nickel plating by means of a rack is suitable for large and bulky workpieces or for precision components. The components are hung up or fitted on a rack and guided carefully through the process.
Sealing
Sealing provides protection to porous component surfaces. It is suitable, for example, for castings. A transparent organic protective film increases corrosion resistance, thus reducing the workpiece’s sensitivity to fingerprints and also improving its appearance.
Advantages
Electroless nickel plating offers a number of important advantages for the treated components:
- High corrosion protection as well as great hardness and wear resistance
- Hardness and wear resistance can be further improved through a heat treatment
- Desired properties can be precisely controlled by means of the phosphorus content (e.g. hardness, ductility, magnetic properties, etc.)
- Uniform coating thickness even for workpieces with a complex geometry
- High reproducibility and series production reliability
- Excellent solderability
- Layer build-up without lead and cadmium
- No need for an external power source
Areas of application
Its extensive application possibilities and wide range of treatable metal types make electroless nickel plating indispensable in many industries:
- Toolmaking
- Mechanical and plant engineering (e.g. robotics)
- Automotive and aviation (e.g. drive & control technology)
- Electrical industry & microelectronics (e.g. heat sinks, connectors, batteries, and components to be soldered)
- Medical engineering
Suitable materials
In principle, all metallic base materials are suitable for electroless nickel plating. In addition to steel and stainless steel, these materials include aluminium, zinc die-cast, and non-ferrous metals such as copper, brass and bronze, as well as other materials based on sample coatings.
Comparison of the equipment technology: Electroless and galvanic nickel plating
During electroless nickel plating, nickel ions are transferred from the bath into the workpiece. A stable nickel content and the appropriate pH value are ensured by top-up pumps and regular checks. The age of the bath is indicated by the metal turnover (MTO). A constant temperature of 90 °C must be maintained. After one to two weeks, it is necessary to prepare a completely new bath.
This elaborate bath management paired with the long process duration makes electroless nickel plating costly, with more complex equipment technology than that used for galvanic processes.
Good to know: Electroless nickel is known by a multitude of names
Besides chemical nickel plating and chemical nickel coating, which both indicate the chemical nature of the process, the process is known by a number of other names, such as electroless nickel ("EN" for short). With regard to the elements contained, the terms nickel-phosphorus alloy or, for short, "nickel phosphorus" or "NiP", have become established. Other distinguishing terms are low-phosphorus/Low-Phos, medium-phosphorus/Mid-Phos, and nickel high-phosphorus/High-Phos, which are indicative of the phosphorus content.
System size & processing options
The dimensions of our system are:
Length: 2,100 mm
Width: 1,150 mm
Height: 730 mm
We can process barrel goods Special dimensions upon request
Process locations
At Härtha, we offer electroless nickel plating at various locations. Learn more in our location overview.
Customer information
Would you like us to treat your components with electroless nickel plating? Please start by providing us with the material designation and information about thermal pre-treatments (if applicable). We will then get back to you.