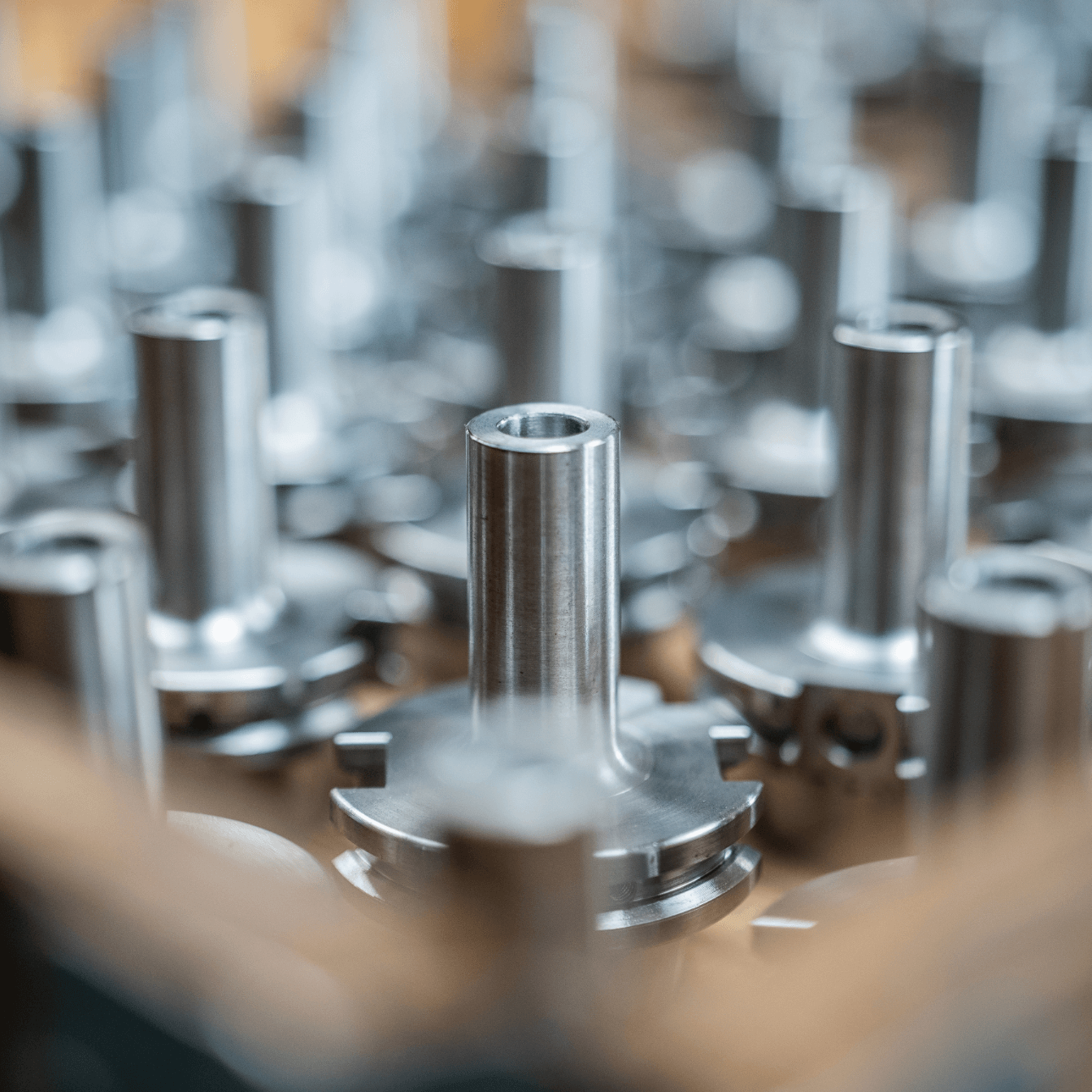
Das Verfahren: Wie wird chemisch vernickelt?
Die chemische Vernickelung ist eine maßhaltige Beschichtungsmethode für fast alle Metallsorten. Ein außenstromloser chemischer Prozess bei einer Temperatur von etwa 90 °C sorgt für die Abscheidung der Chemisch-Nickel-Schicht. Dabei stellt sich eine gleichmäßige Verteilung der Schichtdicke auf dem gesamten Werkstück ein.
Die chemische Vernickelung ist sehr zeitintensiv und entsprechend teuer. Man benötigt in etwa eine Stunde für 10 μm Chemisch Nickel. Dickere Schichten als 50 μm sind in der Praxis daher selten.
INFO: Unterschied zum Galvanisch Nickel
Zur Abscheidung von Nickelionen aus dem Metall sind Elektronen notwendig. Beim Galvanisch Nickel wird dazu von außen elektrischer Strom zugeführt, zum Beispiel aus einem Gleichrichter. Beim Chemisch Nickel werden die Elektronen hingegen durch eine Redoxreaktion im Bad selbst erzeugt. Das ermöglicht konturentreue Beschichtungen mit einer Toleranz von ± 2 μm bis ± 3 μm bei einer Schichtdicke von 8 μm bis 80 μm. Ab 50 μm können sich allerdings Spannungen in der Chemisch-Nickel-Schicht bilden.
Schichteigenschaften
Über die Phosphorkonzentration können die Eigenschaften der Nickel-Phosphor-Schicht gezielt gesteuert werden. Bei 3 % bis 7 % spricht man von einem niedrigen Phosphorgehalt, 6 % bis 9 % sind ein mittlerer Phosphorgehalt und 10 % bis 12 % sind ein hoher Phosphorgehalt.
- Je höher der Phosphorgehalt, desto höher fällt der Korrosionsschutz aus. Wichtig ist auch die Porenfreiheit der Schicht. Diese ist abhängig von der Werkstoffsorte und Vorbearbeitungen des Werkstücks (Fräsen, Polieren etc.), weil diese die Haftfestigkeit beeinflussen. Die Dicke der Korrosionsschutzschicht beträgt in der Regel mindestens 30 μm bis 50 μm.
- Je geringer der Phosphorgehalt, desto höher steigt die Härte bzw. die Verschleißfestigkeit. Durch eine zusätzliche Wärmebehandlung (bis zu einer Stunde bei maximal 400 °C) können 800 HV bis 1.100 HV erreicht werden. Zwischen 10 μm und 50 μm Schichtdicke sind üblich.
Die Optik der Chemisch-Nickel-Schicht lässt sich nur bedingt gestalten, zum Beispiel durch Glanzbildner im Elektrolyt. Einstellbare Eigenschaften wie die Korngrenzendichte können das Aussehen in geringem Ausmaß beeinflussen. Die Optik hängt also im Wesentlichen von der Vorbearbeitung des Werkstücks ab – glänzende Oberflächen bleiben glänzend, matte Oberflächen bleiben matt.
Auch die Haftfestigkeit ist abhängig von der Werkstoffsorte und von vorherigen
Bearbeitungen. Eine Wärmebehandlung bei geringen Temperaturen und langer Haltezeit verbessert die Haftfestigkeit.
Verfahrensarten
Mid-Phos Chemisch Vernickeln
(Mittlerer Phosphorgehalt)
Bei Chemisch Nickel Mid-Phos wird ein mittlerer Phosphorgehalt (6 % bis 9 %) erreicht. Es wird angewendet, um die Härte (ca. 600 HV) und Verschleißfestigkeit von Werkstücken zu steigern und einen guten Korrosionsschutz (über 480 Stunden bei s/min = 0,030 mm) zu erreichen. Die Werkstücke werden ferromagnetisch. Durch eine Wärmebehandlung kann die Härte auf ca. 1.000 HV erhöht werden.
High-Phos Chemisch Vernickeln
(Hoher Phosphorgehalt)
Bei Chemisch Nickel High-Phos stellt sich ein hoher Phosphorgehalt (10 % bis 12 %) ein. Dieses Verfahren ist ideal für Werkstücke, die eine sehr hohe Korrosionsbeständigkeit (über 500 Stunden bei s/min = 0,030 mm) aufweisen sollen und nicht magnetisch sein dürfen. Verschleißfestigkeit und Härte (ca. 550 HV) sind geringer als beim Mid-Phos-Verfahren. Auch hier kann eine thermische Nachbehandlung zu einer höheren Härte (ca. 900 HV) verhelfen.
Thermische Behandlung
Eine thermische Nachbehandlung chemisch vernickelter Werkstücke dient in erster Linie zur Härtesteigerung auf bis zu 1.000 (± 50) HV; außerdem zur Verbesserung der Verschleißfestigkeit und Erhöhung der Schichthaftung. Dazu werden die Werkstücke bei 230 °C bis 400 °C getempert.
Hybridbeschichtung
Die Hybridbeschichtung vereint sämtliche Vorteile der Verfahren Chemisch Nickel und Hartchrom. Nach der chemischen Vernickelung folgt das Hartverchromen. So entsteht ein Schichtsystem mit einem sehr guten Korrosionsschutz und einer sehr hohen Verschleißfestigkeit. Die jeweilige Schichtdicke orientiert sich am Anwendungszweck. Werkstücke mit Hybridbeschichtung eignen sich für die Nutzung in rauen Umgebungen mit hohen chemischen und mechanischen Belastungen.
Trommelbeschichten
Beim Trommelbeschichten befinden sich die Werkstücke in einer perforierten Trommel, die sich um die eigene Achse dreht. Durch die Rotation werden alle Werkstücke gleichmäßig behandelt. Dieses Verfahren wird für Schüttware wie zum Beispiel Schraubverbinder eingesetzt.
Gestellbeschichten
Die chemische Vernickelung mittels eines Gestells eignet sich für große und sperrige Werkstücke oder Präzisionsbauteile. Diese werden am Gestell aufgehangen oder darauf gesteckt und vorsichtig durch das Verfahren geführt.
Versiegelung
Eine Versiegelung bietet porösen Bauteiloberflächen Schutz. Sie eignet sich zum Beispiel für Gussteile. Ein transparenter organischer Schutzfilm erhöht die Korrosionsbeständigkeit, verringert folglich die Griffempfindlichkeit und verbessert nebenbei das Aussehen.
Vorteile
Chemisch Vernickeln bietet eine Reihe wichtiger Vorteile für die behandelten Bauteile:
- Hoher Korrosionsschutz sowie hohe Härte und Verschleißfestigkeit
- Härte und Verschleißfestigkeit können durch Wärmebehandlung weiter verbessert werden
- Gewünschte Eigenschaften können über den Phosphorgehalt präzise gesteuert werden (z.B. Härte, Duktilität, magnetische Eigenschaften)
- Gleichmäßige Schichtdicke auch bei Werkstücken mit komplexer Geometrie
- Hohe Reproduzierbarkeit und Seriensicherheit
- Sehr gute Lötfähigkeit
- Schichtaufbau ohne Blei und Cadmium
- Keine externe Stromquelle notwendig
Anwendungsbereiche
Die umfangreichen Einsatzmöglichkeiten und behandelbaren Metallsorten machen Chemisch Nickel für viele Branchen unverzichtbar:
- Werkzeugbau
- Maschinen- und Anlagenbau (z.B. Robotik)
- Automobil und Luftfahrt (z.B. Antriebs- & Steuerungstechnik)
- Elektroindustrie & Mikroelektronik (z.B. Kühlkörper, Steckverbinder, Batterien, zu lötende Bauteile)
- Medizintechnik
Geeignete Werkstoffe
Grundsätzlich eignen sich alle metallischen Grundwerkstoffe zum Chemisch Vernickeln. Das umfasst neben Stahl und Edelstahl auch Aluminium, Zink-Druckguss und Buntmetalle wie Kupfer, Messing und Bronze sowie weitere Werkstoffe nach Musterbeschichtung.
Vergleich der Anlagentechnik: Chemisch Nickel und galvanisches Verfahren
Bei der chemischen Vernickelung werden Nickelionen aus dem Bad ins Werkstück eingebracht. Einen stabilen Nickelgehalt und den passenden ph-Wert gewährleisten Nachdosierpumpen und regelmäßige Kontrollen. Der Metall Turn Over (MTO) gibt das Badalter an. Es muss eine konstante Temperatur von 90 °C beibehalten werden. Nach ein bis zwei Wochen wird das Bad komplett neu angesetzt.
Diese aufwendige Badführung und die lange Verfahrensdauer machen Chemisch Nickel zu einem kostspieligeren Verfahren mit komplexerer Anlagentechnik als galvanische Verfahren.
Gut zu wissen: Chemisch Nickel ist unter eine Vielzahl an Namen geläufig
Neben Chemisch Nickel und chemisch Vernickeln, die beide auf die chemische Natur des Verfahrens hinweisen, gibt es noch eine Reihe weiterer Begriffe für dieses Verfahren, wie zum Beispiel die englische Bezeichnung Electroless Nickel (kurz EN). In Hinblick auf die enthaltenen Elemente hat sich auch der Begriff Nickel-Phosphor-Legierung, kurz Nickel Phosphor bzw. NiP, etabliert. Zudem werden Niedrigphosphor/Low Phos, Mittelphosphor/Mid Phos und Nickel Hochphosphor/High Phos nach Phosphorgehalt unterschieden.
Anlagengröße & Bearbeitungsmöglichkeiten
Die Abmessungen unserer Anlage sind:
Länge: 2.100 mm
Breite: 1.150 mm
Höhe: 730 mm
Wir können Trommelware behandeln und Spezialmaße auf Anfrage.
Verfahrensstandorte
Bei Härtha bieten wir die chemische Vernickelung an verschiedenen Standorten an. Erfahren Sie mehr in unserer Standortübersicht.
Kundenangaben
Sie wollen Bauteile bei uns chemisch vernickeln lassen? Bitte teilen Sie uns zunächst die Werkstoffbezeichnung und thermische Vorbehandlungen mit (falls erfolgt). Unsere Spezialisten melden sich umgehend bei Ihnen.