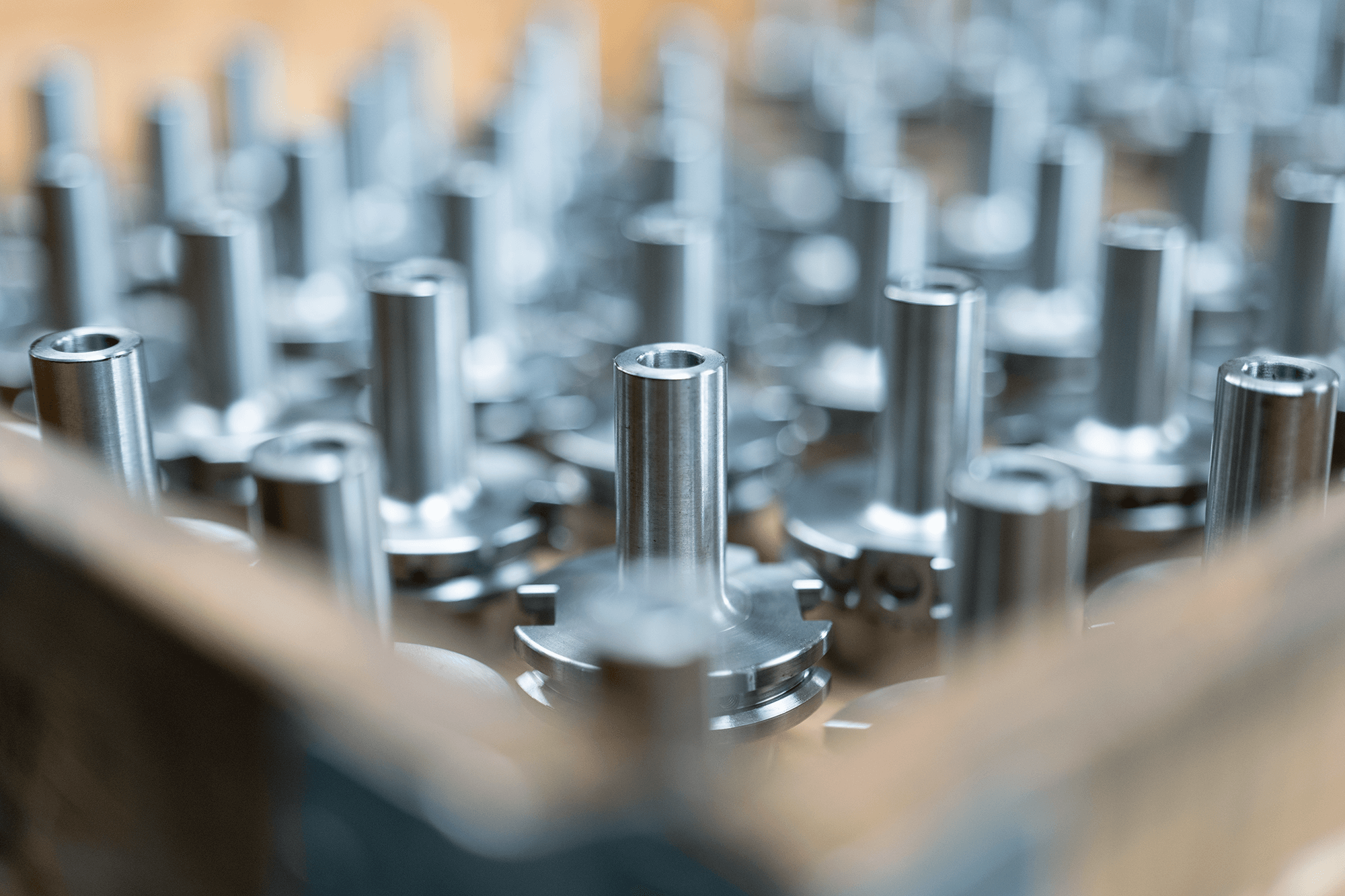
The process/process flow
Anodising is divided into three phases - pre-treatment, anodic oxidation, and sealing. The use of a dye bath is a further optional step, and is performed before sealing, when dyeing of the workpiece is desired.
Pre-treatment
So that the workpiece surface is optimally prepared for oxidation, it is first thoroughly cleaned and freed of dust and grease. In addition, thermal pre-treatments such as hot bending or welding can cause changes in the material that carry over to the anodised coating. Chemical pickling can even out these irregularities and achieve the most homogeneous microstructure possible. DIN 17611 defines all methods of pre-treatment for anodising.
Anodic oxidation
The actual electrolytic oxidation process, carried out in an electrolyte bath, now follows. In this step, the aluminium workpiece is immersed in oxalic or sulphuric acid. At the same time, an anodic circuit is created by a connection with the positive terminal of a DC source. In addition, a cathode is used for this step. The electrodes used are usually plates made of titanium or lead, because they are passive to the electrolyte. Electrolysis now splits the water into hydrogen and oxygen. The hydrogen escapes at the cathode, and the oxygen reacts with the aluminium of the anode.
A thin barrier layer is formed, continually growing into the aluminium. Capillary-like pores develop.In the end, about a third of the anodised coating protrudes beyond the original surface level of the workpiece.
Dyeing
Once all residual acid has been removed, the workpiece can be dipped in a dye bath. The open pores absorb the dye, and so it is well protected against abrasion. This process may take up to 20 minutes. Common colours are gold, purple, blue, red and green, as well as black. It is not possible to colour the material white.
Sealing
In the final step , the workpiece is boiled in demineralised water. This forms a transparent alumina hydrate, which closes the remaining pores on the surface of the anodised coating.
Basic technical principles
The DIN 8580 standard classifies anodising as a coating process. More specifically, it is a galvanic coating applied by means of electrolytic oxidation of aluminium.
Aluminium naturally reacts with the oxygen in the air to form aluminium oxide. This reaction creates a transparent oxide layer on the surface which is a few nanometres thick and protects against corrosion. Hardness and wear resistance remain unaffected.
Electrolytic oxidation is used to enhance this layer formation, making it possible to achieve coating thicknesses of 5 μm to 25 μm. As long as the workpiece surface remains unharmed, this coating reliably protects the workpiece from corrosion.
The hardness levels that can be achieved with anodising range between 200 HV and 400 HV. The hard electrolytic oxidation process produces hardness levels up to 600 HV. In addition, the anodised coating can be dyed for decorative purposes.
INFO: What metals can be anodised?
Anodising is possible only with aluminium. This is indicated by the acronym
"Eloxal", which stands for "electrolytic oxidation of aluminium" and is often used as a synonym. In the case of ferrous metals, oxidation will result in rusting rather than in a refinement of the surface. For such metals, other types of surface refinement are used. One example is the burnishing of steel.
Features and advantages
Anodising provides a number of key advantages for aluminium components:
- High corrosion resistance for outdoor use
- Scratch-resistant, hard surface without peeling
- Decorative properties
- Low coating thickness
- Electrical insulation
Areas of application
The main purpose of the electrolytic oxidation process is the corrosion protection of aluminium semi-finished products, such as sheets, rods, pipes, and profiles. However, the dyeing process is also frequently applied for decorative purposes, for example for fasteners such as snap hooks.
INFO: Additives to alloy components
The basic prerequisite for successful electrolytic oxidation is a material having electrolytic oxidation quality, "EQ" for short. Conversely, anodising may lead to structural changes or staining if used on cast aluminium or similar alloys. Examples of materials commonly subjected to anodising are AlMg 1 hh EQ or AlMgSi 0.5 EQ.
Oxide layer and coating formation processes
For problem-free coating formation during anodising, no foreign metals must be trapped in the aluminium, and any roughness must have been removed from the aluminium surface.
The properties of the anodised coating depend on the temperature, current density, and voltage, and also on the composition of the electrolyte. While the base material of the anodised coating is always aluminium oxide, adding chemical additives to the electrolyte can improve properties such as durability.
Another factor playing a major role is the use of direct current or alternating current. The coating thickness is essentially influenced by the duration of the treatment.
Unlike aluminium, aluminium oxide does not conduct electricity. The oxide layer thus affects the insulation capability of the workpiece.
Cleaning anodised aluminium
Anodised aluminium rarely requires any maintenance. If used in a normal environment, the material needs to be cleaned only once per year - in rough conditions, twice per year. To preserve the surface, it is advisable to use pH-neutral cleaning agents.
Anodising vs. powder coating
While powder coating conceals the surface structure of a workpiece, this remains largely discernible after anodising, because the anodised coating is only a few nanometres thick. In addition, the coating is matt.
System size:
1,600 x 600 x 900 mm
Process locations
The Härtha hardening plant operates subsidiaries spread throughout Germany and Europe. Refer to our location overview to learn at which locations we perform anodising.
Customer specifications for anodising
We will be glad to send you a non-binding proposal for our anodising services. Before we can do so, we need the corresponding material designation. We will then send you our response by return, with additional information.