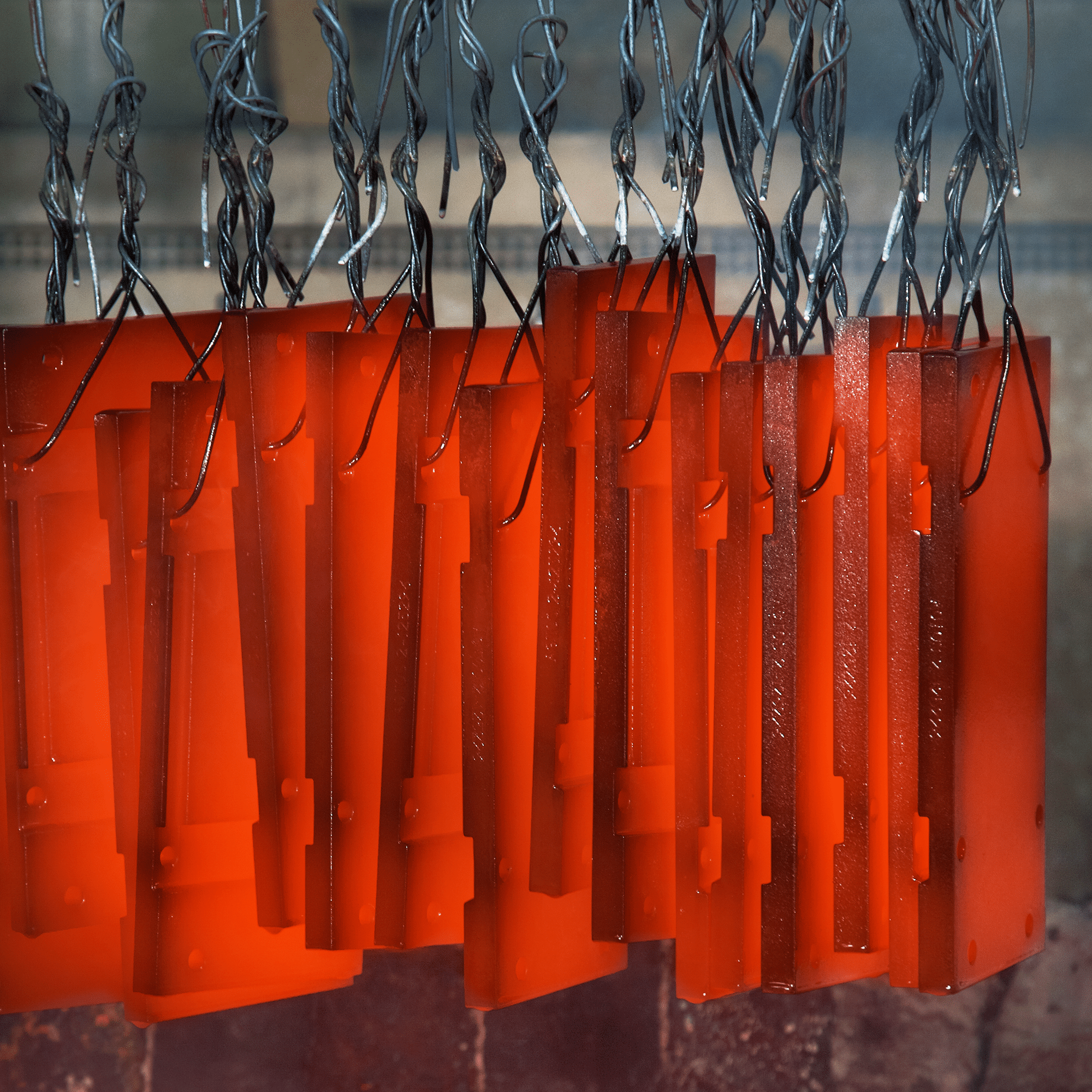
Das Verfahren und seine Vorteile
Mit dem schonenden Salzbadhärten sollen eine möglichst verzugsarme Härtesteigerung und eine höhere Verschleißbeständigkeit erreicht werden. Dabei können sowohl die Erwärmung als auch die Abkühlung in einer Salzschmelze stattfinden. Häufig kommen Cyanide als Schmelzsalze zum Einsatz, aber auch Bariumsalze und spezielle Anlasssalze zum Anlassen.
Die Temperatur der Salzschmelze (z.B. beim Salzbadnitrieren) bewegt sich in der Regel zwischen 150 °C und 1.300 °C. Für die Erwärmung von Metall sind Temperaturen zwischen 800 °C und 1.200 °C typisch. Zum Abschrecken im Warmbad eignen sich Temperaturen zwischen 140 °C und 250 °C (bei abgestuftem Abschrecken bis zu 450 °C).
Ihre Temperaturstabilität und ein weicher Wärmeübergang machen Salzschmelzen attraktiv für Glüh- und Härteverfahren. Durch die langsame Abkühlung bilden sich keine Dampfblasen auf der Bauteiloberfläche. Zudem lagert sich ein Salzfilm auf dem Werkstück ab, der ungewollte Abkühleffekte wie die Randentkohlung verhindert.
Zusammenfassung: Vorteile auf einen Blick
- Besonders gleichmäßige Wärmezufuhr
- Reduzierte Rissbildung
- Geringer Verzug
- Keine Randentkohlung
- Optimierung der Verschleißbeständigkeit
- Hohe Reproduzierbarkeit
Das Salzbadhärten zeichnet sich als besonders flexibles und zuverlässiges Verfahren aus. Unsere Experten bei Härtha beraten Sie gerne zu den Details.
Info
Aufgrund der Giftigkeit der eingesetzten Salze gilt Salzbadhärten fälschlicherweise als überholt, obwohl es in der Industrie nach wie vor an der Tagesordnung ist. Moderne Verfahren und schonendere Salze gewährleisten heute eine bessere Recyclebarkeit und Umweltverträglichkeit.
Anwendungen und Werkstoffe
Das Salzbadhärten wird gerne für Bauteile mit komplizierter Form verwendet, die starke Unterschiede im Querschnitt und im Gewicht aufweisen. Das können zum Beispiel Wellen, Zahnräder oder Werkzeuge sein.
In solchen Fällen können durch partielles Härten verschiedene Bereiche unterschiedlich stark gehärtet werden. Dazu eignet sich eine Wärmebehandlung in der Salzschmelze. Durch den langsamen Abschreckungsprozess kann zudem eine ausgeglichene Temperaturverteilung in den unterschiedlichen Bereichen des Bauteils sichergestellt werden, die Spannungen minimiert.
Geeignete Werkstoffe
Werkzeugstähle und Federstähle bzw. legierte Stähle werden häufig durch Salzbadhärten behandelt. Grundsätzlich eignen sich alle Stahlsorten zum Salzbadhärten, die auch für das Ölbadhärten geeignet sind. Weitere Komponenten, wie die Größe und der Aufbau der Werkstücke sowie die Sollhärte und -zähigkeit, sind entscheidend.
Ein Auszug der Stahlsorten, die sich für eine Salzbadbehandlung eignen:
Werkstoffnummer | Kurzname |
1.1273 | 90Mn4 |
1.7225 | 42CrMo4 |
1.3505 | 100Cr6 |
1.0762 | 44SMn28 |
1.7228 | 50CrMo4 |
1.6511 | 34CrNiMo6 |
1.6582 | 43CrNiMo6 |
1.7006 | 46Cr2 |
1.7035 | 41Cr4 |
1.8159 | 50CrV4 |
1.6545 | 30NiCrMo2 |
1.6546 | 40NiCrMo2 |
Anwendungsgebiete
- Werkzeug- und Maschinenbau
- Luft- und Raumfahrt
- Automobilbranche
Verfahrensstandorte
Unsere Standorte in Deutschland und Europa finden Sie hier.
Unsere Anlage
Durchmesser:
600 mm x 500 mm
Max. Gewicht:
500 kg
Maximale Arbeitstemperatur:
1.200 °C
Sie möchten bei uns Salzbadhärten?
Dann benötigen wir von Ihnen folgende Angaben:
- Werkstoffbezeichnung
- Sollhärte mit Toleranzbereich
- Maximal zulässiger Verzug
- Zusätzlich gewünschte Vor- und Nachbehandlungen
- Prüfbereich falls vorgeschrieben