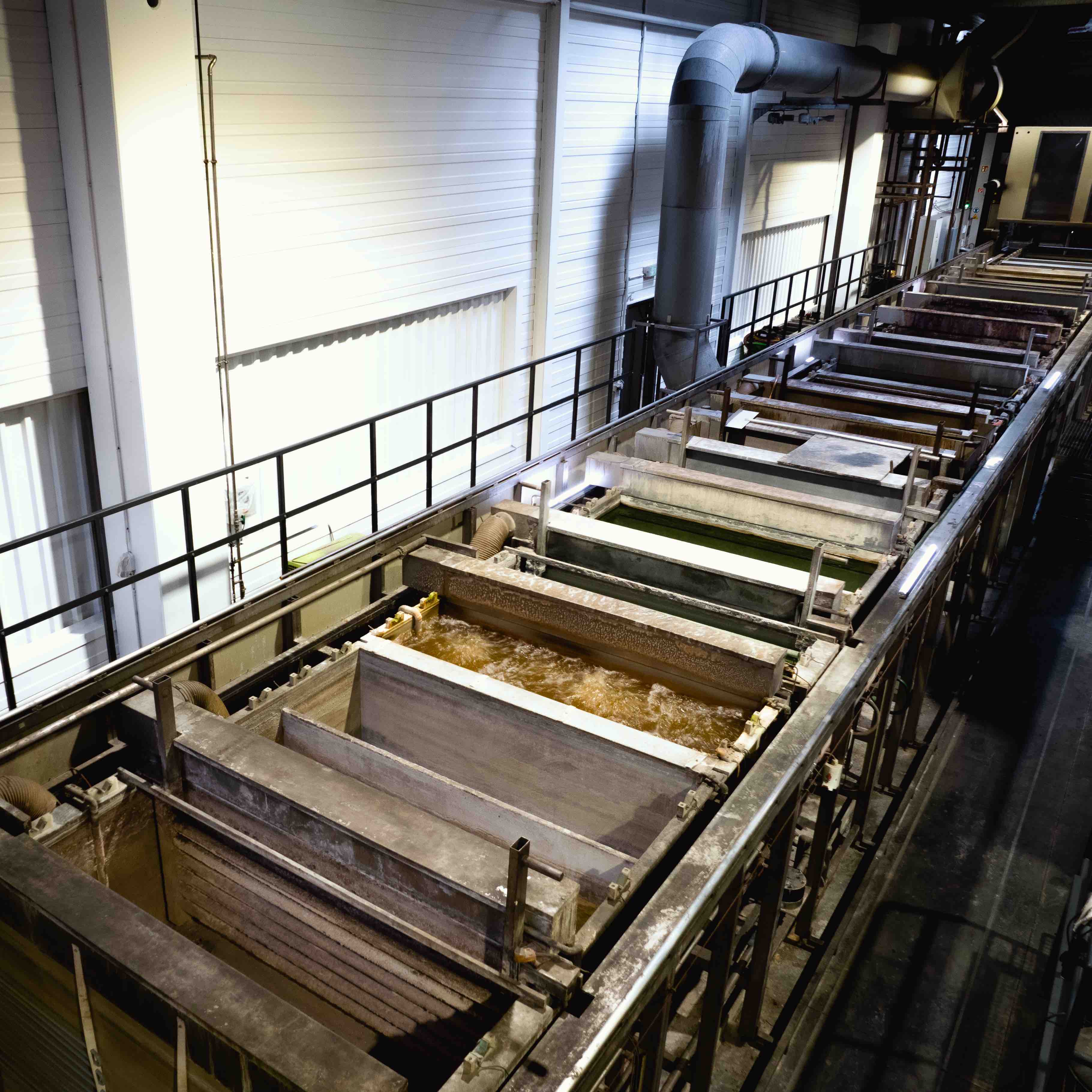
Il processo
Lo scopo della fosfatazione è quello di formare uno strato di fosfato sulla superficie metallica. Prima di tutto il componente viene sottoposto a decapaggio in modo da eliminare lo strato di ossido naturalmente presente sul metallo. Così facendo i cationi metallici si sciolgono sviluppando idrogeno.
Segue quindi il bagno in una soluzione di fosfato durante il quale i fosfati scarsamente solubili precipitano. A seconda della composizione della soluzione, si forma uno strato di fosfato di ferro, manganese o zinco. Il processo può eventualmente essere ripetuto. Esiste la fosfatazione con e senza formazione di strato.
Fosfatazione senza formazione di strato
La fosfatazione senza formazione di strato è così chiamata in quanto nessun catione metallico viene trasferito dalla soluzione di fosfato al metallo da trattare. Tutti i cationi per la formazione dello strato provengono dal materiale stesso. Ciò consente un'elevata precisione dimensionale, ma offre una minore protezione contro la corrosione rispetto alla fosfatazione con formazione di strato.
Fosfatazione con formazione di strato
Nella variante di fosfatazione con formazione di strato, nella generazione dello strato possono essere coinvolti anche cationi provenienti dal metallo base, anche se la maggior parte dei cationi metallici proviene dalla soluzione di fosfato. Per i pezzi ad accoppiamento è necessario tenere in considerazione lo strato aggiuntivo, il cui spessore può variare da qualche centinaio di nanometri a pochi micrometri.
Metalli e tipologie
Un'altra caratteristica distintiva della fosfatazione è data dal metallo che contribuisce alla formazione dello strato – solitamente ferro, zinco o manganese. A seconda delle proprietà desiderate, è anche possibile applicare contemporaneamente due o tre di questi metalli.
Ferro
La fosfatazione al ferro viene utilizzata per la protezione dalla corrosione e come base per la verniciatura di componenti, come ad esempio le lamiere. Viene considerata la variante più semplice ed economica, in quanto l'attivazione e la fosfatazione avvengono nello stesso passaggio. Per la fosfatazione al ferro sono necessarie temperature da 25 °C a 65 °C e valori pH compresi tra 4 e 6. Gli strati di fosfato di ferro pesano tra 0,2 e 0,8 g/m². La fosfatazione al ferro è adatta per pezzi in ferro, alluminio e zinco.
Zinco
Nella fosfatazione allo zinco, la superficie metallica deve essere pretrattata in modo da ottenere uno strato di fosfato di zinco finemente cristallino. Si procede poi al bagno a base di sali di titanio. Al successivo bagno a 35 °C - 80 °C e con valori pH di 2,2 - 3,2 si aggiunge nichel. Durante questo processo si formano sulla superficie metallica dei pori che assorbono molto bene gli oli anticorrosione. Migliora anche l'adesione della vernice sull’acciaio, sia nudo che zincato. Lo strato in fosfato di zinco è opaco e il colore va dal grigio chiaro al grigio medio. Il peso è compreso tra 1,5 e 30 g/m².
Manganese
La fosfatazione al manganese è condotta a temperature comprese tra 90 °C e 95 °C e con un pH compreso tra 2,2 e 2,4. Gli strati di fosfato di manganese pesano tra 10 e 25 g/m². Offrono proprietà di riduzione dell'attrito, buona protezione dalla corrosione e un'elevata capacità di assorbimento dell'olio - pertanto sono ideali per l'uso su ingranaggi o cuscinetti radenti. Per il suo colore, da grigio scuro a nero e la finitura satinata, la fosfatazione al manganese viene utilizzata anche per migliorare l'estetica delle armi da fuoco portatili.
INFORMAZIONI: spessore dello strato
Lo composizione della soluzione di fosfato determina lo spessore dello strato di conversione. Mentre le fosfatazioni al manganese o allo zinco possono avere spessori fino a 2 µm, di norma gli strati della fosfatazione al ferro sono spessi solamente qualche centinaio di nanometri.
Altri metalli e tipologie
La fosfatazione tricationica è un processo di fosfatazione allo zinco-nichel-manganese. Nitrato di sodio, nitrito di sodio, fluoruro di sodio e calcio sono altri additivi spesso usati per la fosfatazione. Meno comune è invece l’uso di titanio, zirconio e solfato di rame. Il nichel è stato invece eliminato quasi del tutto per gli effetti nocivi per la salute.
Caratteristiche e vantaggi
- Promotore di adesione: lo strato di fosfato è saldamente ancorato al metallo base
- Protezione anticorrosione elevata: pori e capillari assicurano un'elevata capacità di assorbimento di oli e vernici anticorrosivi
- Elevata scorrevolezza: riduzione di attrito e usura
- L'aspetto può essere adattato a seconda del processo: struttura con grana da cristallina fine a cristallina grossa, colore da grigio chiaro a nero
- Isolamento: gli strati di fosfato offrono una resistenza di isolamento elevata
- Resistenza alla ruggine: gli strati danneggiati sono poco predisposti all’ossidazione
Campi di impiego
La fosfatazione viene usata spesso sull’acciaio, ma anche sull’alluminio e per gli acciai zincati e cadmiati. Serve principalmente quale preparazione per il rivestimento. Poiché lo strato di fosfato aderisce molto bene alle superfici metalliche e i suoi pori o capillari costituiscono la base perfetta per oli, grassi e vernici, viene usato come promotore dell’adesione.
Fosfatazione come protezione anticorrosione
Lo strato di fosfato offre già di per sé una protezione dalla corrosione che può essere ulteriormente migliorata, ad esempio, mediante ceratura o oliatura. Inoltre, lo strato è resistente alla ruggine ed è in grado di prevenire in larga misura le infiltrazioni della ruggine sottostante. La fosfatazione allo zinco è più resistente alla corrosione rispetto a quella al ferro.
Miglioramento delle proprietà di scorrimento grazie agli strati di fosfato
La fosfatazione migliora le proprietà di scorrimento dei pezzi. Gli strati di fosfato di zinco vengono utilizzati in particolare per la deformazione a freddo dell'acciaio. Reagiscono con saponi alcalini formando saponi di zinco che resistono a temperature più elevate e costituiscono un sistema lubrificante ideale.
Per evitare grippaggi dei pezzi per l'assenza di lubrificante, spesso si usano anche strati di fosfato di manganese, che sono in grado di ridurre l’usura delle superfici soggette ad attrito.
Proprietà elettriche
Gli strati di fosfato sono ideali per l'isolamento in quanto offrono un'elevata resistenza elettrica abbinata a spessori minimi. Vengono utilizzati, ad esempio, per le lamiere per nuclei magnetici.
Confronto: fosfatazione contrapposta alla brunitura
Gli strati di fosfato offrono una protezione dalla corrosione migliore rispetto a quelli di brunitura, in quanto i loro contorni irregolari assicurano una migliore adesione degli oli e dei grassi anticorrosivi rispetto alle superfici di brunitura amorfe.
Grazie all'elevata precisione dimensionale, la brunitura è particolarmente adatta per parti di precisione, in quanto lo strato si forma all'interno della superficie del componente. Nella fosfatazione con formazione di strato, tuttavia, si deve tenere conto dello spessore dello strato generato sulla superficie.
La speciale competenza di Härtha
Per la buona riuscita della fosfatazione è essenziale il preciso coordinamento tra temperature, tempi di reazione, prodotti chimici e loro concentrazione. Grazie alla lunga esperienza pratica nella gestione dei bagni e a impianti modernissimi, possiamo garantire la scelta dei parametri migliori. Facciamo in modo che i vostri materiali base non vengano danneggiati e adeguiamo lo spessore dello strato di fosfatazione, le dimensioni dei cristalli e l'aderenza della superficie allo scopo d’impiego dei pezzi. Affidatevi a un partner competente per la massima qualità.
Dimensioni degli impianti
Dimensioni massime dei pezzi:
1.800 x 320 x 500 mm
Indicazioni del cliente per la fosfatazione
Ci fa molto piacere che vogliate commissionare la fosfatazione dei vostri pezzi a Härtha. Abbiamo però bisogno delle seguenti indicazioni:
- Denominazione del materiale
- Eventuali indicazioni sui precedenti trattamenti termici
- Eventuali indicazioni sullo spessore dello strato desiderato (in µm)
Sedi dei processi
La nostra mappa delle sedi indica gli stabilimenti che offrono la fosfatazione e tanti altri processi.