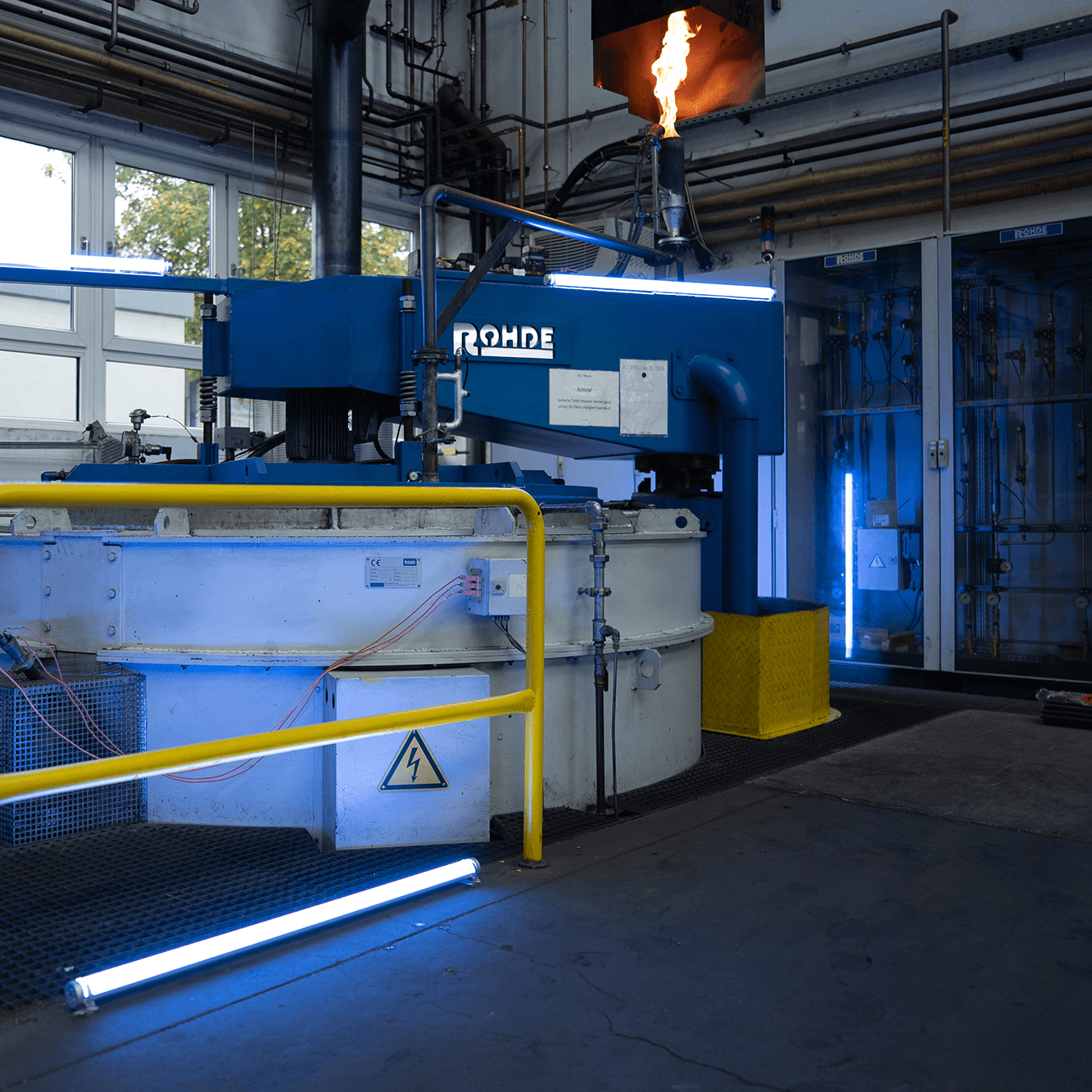
The process and its advantages
Stress-free annealing is used to reduce intrinsic tensions in metallic microstructures. The process prevents the intrinsic stresses in the metal from combining with load stresses that can occur through further processing or use of the workpiece. This protects the workpiece from warping and breakage.
Processes that can lead to intrinsic stresses in the metal include:
- Metal-cutting machining such as turning or milling
- Welding
- Cold forming such as deep drawing or bending
- Uneven cooling caused by, for example, prevention of contraction during casting
- Microstructural transformation
If executed properly, stress-free annealing can generally reduce stresses by up to 90%. Stress-free annealing can take place in a convection furnace.
In order to protect the workpiece surface from oxidation, stress-free annealing is carried out in a protective gas furnace. For applications that impose stringent requirements on the component surface, treatment in a vacuum furnace may also be considered.
Individual phases
Stress-free annealing is essentially divided into three phases: warming up, dwelling, and cooling. During the warm-up time, the material is heated. This warm-up phase is followed by a dwell time that lasts four to six hours at a constant temperature.
The annealing temperature and the annealing time play essential roles in the success of the process. Finally, during the cooling time, the workpiece is slowly cooled in the air or in the furnace, in order to prevent stresses and cracking from reoccurring.
Both the warm-up phase and the cooling phase should be carried out in a slow and controlled manner in accordance with the thermal conductivity of the material. This ensures a low temperature gradient between the surface and the core of the workpiece. If performed too fast, the warm-up or cooling phase can lead to new stresses. This is of particular significance for workpieces with large differences in shape and wall thickness.
The advantages at a glance
The advantages offered by stress-free annealing include:
- Reduction of stresses by more than 90%
- Improved machinability of the material and thus extended service life for tools
- Further processing possible with minimum warping
- Risk of cracking is minimised
- No increased hardness on the component surface
- Greater precision
- Short processing times thanks to low machining allowance
Areas of application
Stress-free annealing is useful after the rough machining of workpieces. It is, for example, suitable for removing stresses from welded structures.
Moreover, this process is a good preparatory measure for the fine machining of workpieces. For example, components having low dimensional tolerances that are to be treated by nitrocarburising must be as tension-free as possible.
Suitable materials and temperatures
The correct annealing temperature is essential for achieving the desired result. It is dependent, among other factors, on the type of material and the pre-treatment. Quenched and tempered steels , for example, are annealed at least 30 °C below the last tempering temperature. Hardened cast irons cannot be annealed at all, because the annealing temperature would trigger a tempering effect.
Untempered castings are suitable for annealing. The correct temperature depends on the alloy composition. For non-alloy grades of cast iron, the temperature is 500 °C to 550 °C, for low-alloy grades, 550 °C to 600 °C, and for high-alloy grades, 600 °C to 650 °C.
Fine grain steels are annealed at temperatures below 580 °C, because they will otherwise experience coarsening of the microstructure. Stainless steels are usually treated using solution annealing.
Copper and brass components can also be treated using stress-free annealing. Depending on the composition of the alloy, the annealing temperature for brass components ranges between 250 °C and 500 °C, and for copper workpieces between 150 °C and 275 °C.
Size of furnace
At Härtha, the systems listed below are available for stress-free annealing:
Convection system: Ø 1010 x 1000 mm
Protective gas/vacuum system: 1200 x 1500 x 800 mm
Process locations
Refer to our location overview to find out which Härtha sites offer stress-free annealing.