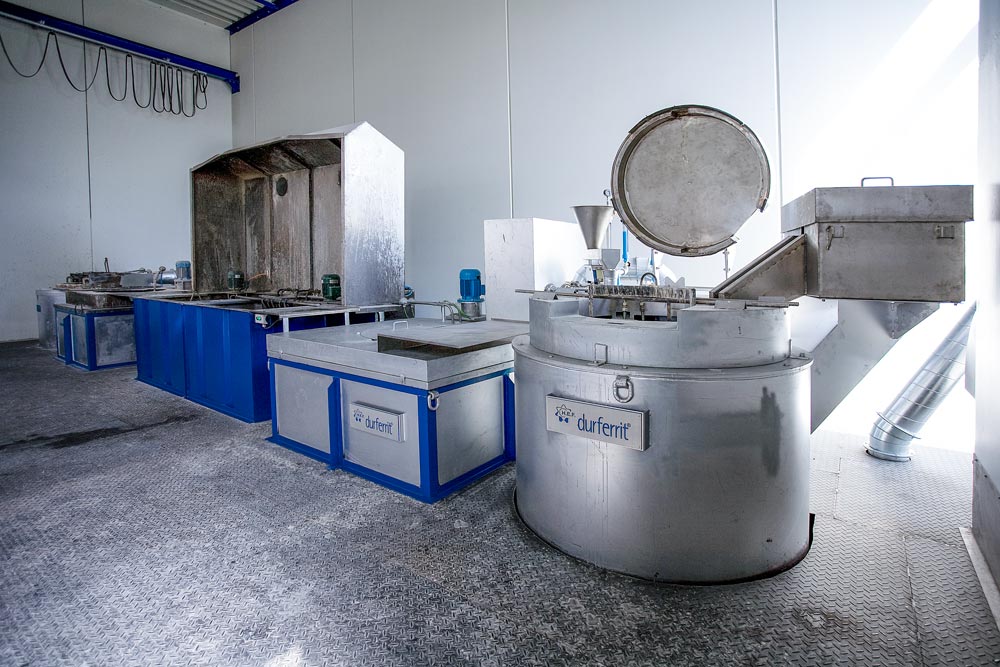
Process and background information
The Tenifer®-QPQ process is based on salt bath nitrocarburising, which involves the diffusion of nitrogen and carbon into the workpiece surface. The process produces a compound layer formed of iron, nitrogen, carbon, and nitrides, which is known for its high wear resistance and low coefficients of friction.
The process comprises four steps:
- Nitrocarburising
- Oxidative quenching
- Mechanical smoothing
- Post-oxidation
This targeted treatment maximises corrosion protection and improves the mechanical stability of the components. Since this procedure is carried out at comparatively low temperatures, changes in size and shape are kept to a minimum. Better yet, it also frequently or completely eliminates the need for costly rework.
The procedures we offer
We offer the following variants of the Tenifer® process:
- Tenifer®-Q: Basic protection against wear, corrosion, and edge-cracking problems, plus heat resistance and durability.
- Tenifer®-QP: Improved surface quality thanks to reduced roughness, lower coefficients of friction, and optimised visual quality of the components.
- Tenifer®-QPQ: Maximum corrosion resistance, decorative black surface, minimum light reflection and superior visual quality.
- Optionale KühlverfahrenThe treatments can be performed by means of water quenching or vacuum gas quenching.
The advantages at a glance
The Tenifer®-QPQ process provides a large number of technical advantages:
- High wear resistance and increased fatigue strength
- Excellent corrosion protection thanks to a layer of magnetite
- Minimum changes in dimensions and shape
- Optimum sliding performance due to the non-metallic properties of the compound layer
- Excellent mechanical resilience
The combination of edge layer hardening and oxidising treatment increases the fatigue strength of the material by up to 100%. At the same time, the treated surface reduces the frictional resistance, resulting in considerably reduced wear, especially in slide and roller bearing applications.
Applications and suitable materials
The Tenifer®-QPQ process is widely used in various industrial sectors:
- Automotive industry (e.g. gearbox components, crankshafts, gears)
- Mechanical engineering (machine parts subject to high loads)
- Aerospace (specialised precision components)
- Medical technology (instruments and components with high standards of hygiene)
- Replacement of coatings containing chrome (VI)
The treatment is suitable for almost all grades of steel and cast materials. Particularly advantageous results are achieved in materials with nitride-forming elements such as chromium, molybdenum, vanadium, and aluminium, as these make enhanced surface hardness possible.
While non-alloy and low-alloy steels achieve the highest level of corrosion protection, the treatment of stainless steels requires special modifications to the process, in order to ensure both optimum hardness characteristics and enhanced corrosion resistance.
Technical requirements for the treatment
To produce optimum results, the Tenifer®-QPQ treatment must be performed under specific process parameters. Besides the exact material designation, it is necessary to specify the temperature of the previous heat treatment, the desired hardness and the desired nitriding hardness depth. If partial treatment is desired, then appropriate drawings are necessary. In addition, to obtain the specified core hardness, the temperature of the previous heat treatment must be at least 20 to 30 degrees Celsius higher than the nitriding temperature.
Conclusion
The Tenifer®-QPQ process combines high wear resistance with excellent corrosion protection and minimum dimensional changes to provide an efficient and environmentally friendly solution for the metalworking industry.
Providing a high-performance alternative to conventional coating procedures, the process is established around the world and suitable for industrial series production, as well as for precision parts subjected to heavy loads. Thanks to its high reproducibility and ease of implementation, it represents a solution that reliably produces durable and resistant components.
Process locations
You will find Härtha in Germany, Italy, and the Netherlands. Refer to our interactive location overview to learn which other processes besides oxidising we offer at locations near you.