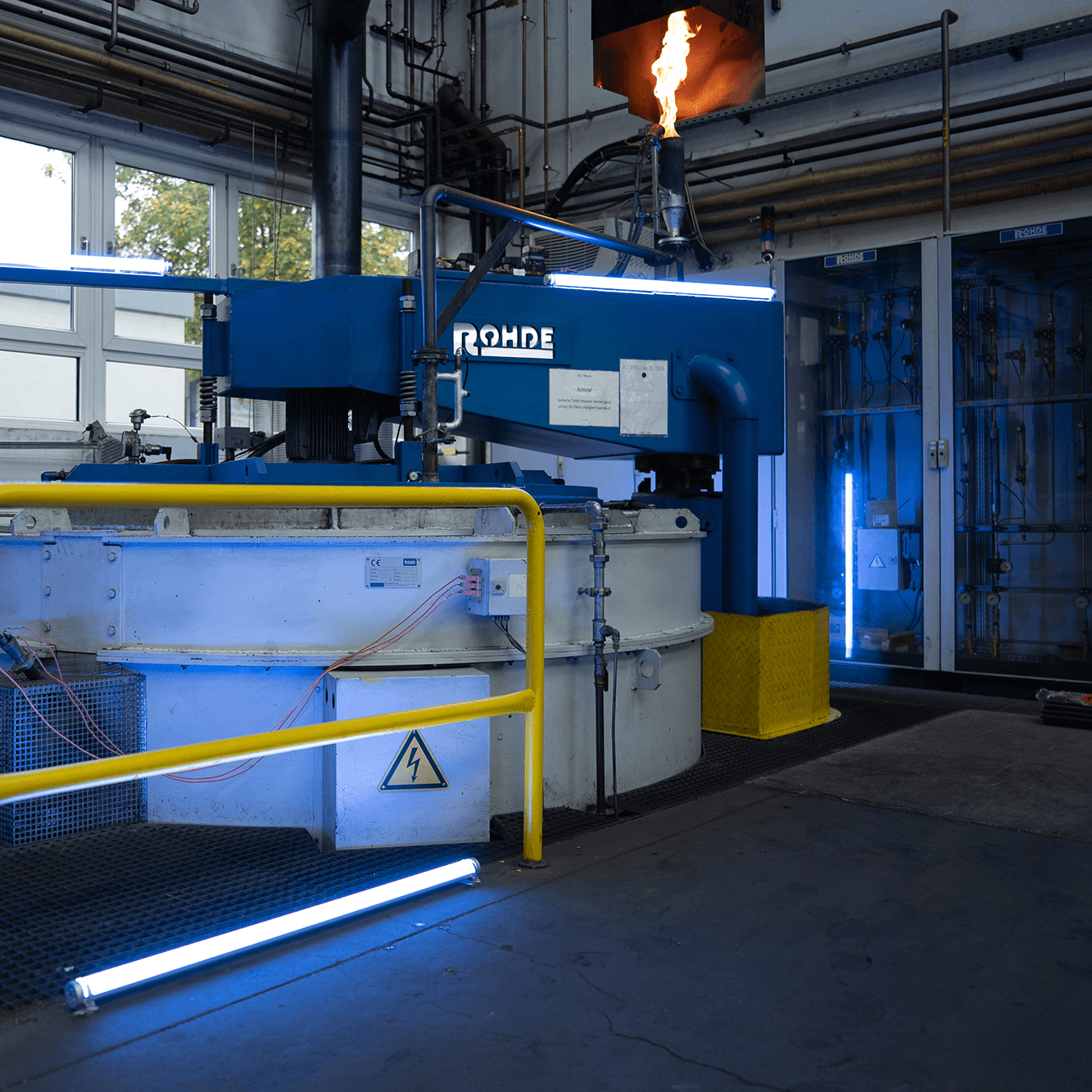
The process and its advantages
The objective of soft annealing is to improve the formability of the workpiece . This requires the original strip-shaped cementite lamellae in the microstructure of the material to be transformed into spherical cementite. Individual spheres present in the microstructure facilitate a dislocation movement, thus improving formability during machining processes such as bending or rolling. Machinability is increased as well. Conversely, the process reduces hardness.
If subjected to hardening prior to soft annealing, the workpiece already has a relatively homogeneous martensite microstructure. This condition allows the formation of a particularly fine spherical cementite, distributed very homogeneously.
In order to protect the material from decarburising and oxidising, soft annealing is carried out in a protective gas furnace or a vacuum furnace.
The whole process may take several hours. Under certain circumstances, the dwell time may have to last up to 100 hours. This depends on the workpiece properties and the annealing temperature.
The correct temperature
The correct temperature for soft annealing depends on the material. For steel alloys, it is normally between 650 °C and 800 °C, for copper between 300 °C and 600 °C, and for brass alloys between 425 °C and 650 °C.
Supra-eutectoid steels can be annealed just above or fluctuating around the PSK line. In contrast, sub-eutectoid steels are heated to just below the PSK line during soft annealing. It is important for the lamellar cementite to not yet decompose. Otherwise, the cementite lamellae will not be able to transform into the desired spherical cementite by means of diffusion.
Temperature range during soft annealing
The advantages at a glance
Soft annealing offers a number of advantages for a workpiece. The most important are:
- A relatively homogeneous microstructure of spherical cementite
- Facilitated dislocation movement in the microstructure
- Good cold formability
- Improved machinability
- Machining tools have an extended service life
Applications and suitable materials
High-carbon steels and tool steels are usually soft annealed to improve their machinability. In addition, soft annealing is used in brass and copper alloys to compensate for the impact of a preceding cold forming process.
Depending on the alloy, different degrees of hardness can be achieved during soft annealing. Types of material typically subjected to soft annealing treatments are:
- Steel 170-300 HB
- Copper 40-70 HV
- Brass 50-100 HV
Negative aspects
If the carbon content of sub-eutectoid steels is below 0.3%, soft annealing is usually not worthwhile, because these grades of steel are already considered relatively soft and easily ductile. Smearing may occur on steels with a carbon content below 0.8%.
Stainless steels with a tantalum or niobium content or a carbon content below 0.04% would lose their rust resistance at temperatures of 400 °C or higher. They must therefore not be subjected to soft annealing.
In addition, soft annealing should not take place prior to induction hardening.
Process locations
Refer to our interactive location overview to find a site close to you that offers soft annealing for your workpieces.