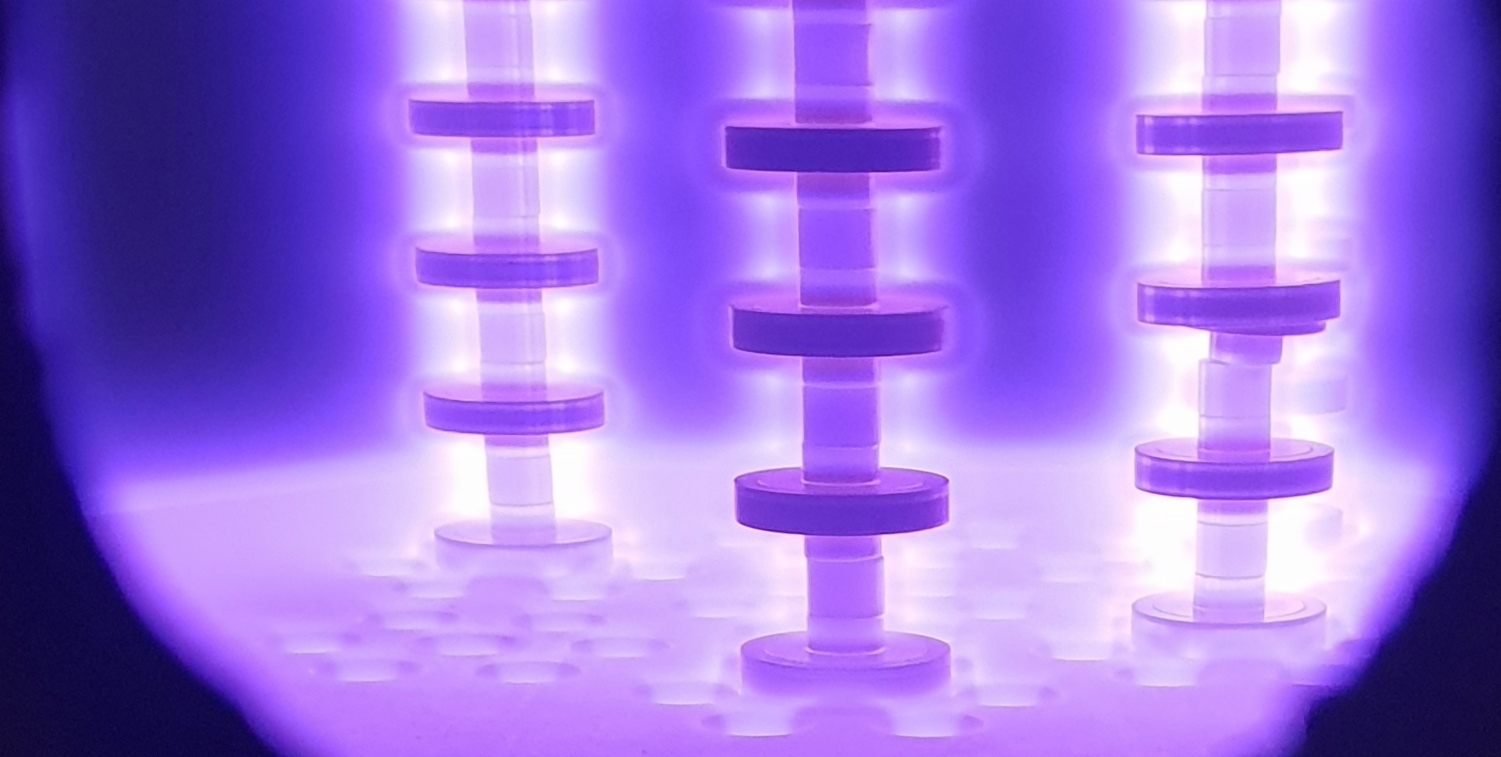
Process & process flow
The PACD process relies on the diffusion of carbon atoms from a carrier gas into the surface layers of the treated component. The process is based on the application of a voltage that generates a plasma of ionised gas in a vacuum. The depth of the diffusion layer can be varied depending on process parameters (temperature, time, and gas composition). The detailed sequence of the process is as follows:
- Preparation of the material: Cleaning the workpiece ensures that it is free of impurities that could compromise the PACD process.
- Vacuum formation: The component enters into a vacuum chamber having a vacuum of 0.1 to 10 millibar. Otherwise, the ambient air would hinder the subsequent plasma formation.
- Gas injection: A gas mixture containing typical carbon carrier gases such as methane or propane is fed into the vacuum chamber.
- Generation of the plasma: High tension from 100 to 1,000 volts is applied between the vacuum chamber and the workpiece. This ionises the injected gas, thus providing the energy necessary for the diffusion of the carbon atoms. The resulting mixture of high-energy ions, electrons and neutral particles forms the plasma.
- Carbon diffusion: The high-energy particles in the plasma remove material atoms from the surface of the workpiece. Simultaneously, they release carbon atoms in the gas, and these can now diffuse into the component surface in accordance with the concentration gradient. This typically happens at temperatures between 300 °C and 400 °C.
- Cooling: After reaching the desired diffusion depth, the plasma is switched off and the workpiece is cooled in a controlled atmosphere in order to further optimise the mechanical properties and prevent oxidation.
Advantages
As well as combining the advantages of other case hardening processes, PACD offers additional benefits:
- Improved surface properties: PACD delivers increased hardness, improved wear resistance and extended fatigue resistance.
- Retention of corrosion resistance: Since this process involves diffusion rather than coating, there is no risk of flaking.
- No increased brittleness: Since it takes place without carbide formation, compared with traditional carburising methods the diffusion results in reduced brittleness of the treated surface.
- Precise process control: The precise control of process parameters such as temperature, pressure and gas composition allows exceedingly uniform carbon distribution and results that can be reproduced at any time.
- Lower temperatures: The lower process temperatures are responsible for minimised grain growth and carbide formation, significantly reducing the risk of warping.
- Environmental performance: Through the use of an enclosed vacuum chamber, PACD generates lower emissions and less environmentally harmful by-products.
- Selective case hardening: Only the workpiece surface is treated, leaving deeper layers unaffected. Moreover, the targeted treatment of certain areas is ideal for workpieces with complex geometries.
- Combination with other processes: PACD can easily be combined with other manufacturing techniques in order to optimise different component properties.
Properties and applications
The thickness of the PACD zone achieved lies between 20 to 40 micrometres, depending on the type of stainless steel and the process parameters. Because the carbon atoms are introduced directly into the material rather than being applied as an additional layer, the corrosion resistance of the surface is retained.
Exceptionally high degrees of hardness can be achieved on the surface. These vary depending on the stainless steel alloy. For example, a surface hardness of over 1,100 HV0.1 can be achieved for the AISI 316 grade of stainless steel.
The positive properties and the relative environmental friendliness of the process make PACD relevant to a wide range of industries and areas of application:
- Industries: Automotive, aerospace, medical equipment, water systems, etc.
- Components: Pumps, transmissions, shafts, surgical instruments, cutting tools
Challenges
The basic prerequisite for PACD case hardening is an understanding of physics, chemistry and material science which allows correct assessment of the interactions between material and process. The following challenges must be mastered:
- Correct process parameters: The proper temperature, treatment duration and gas composition, as well as appropriate pressure, are crucial to achieving all the desired properties on the workpiece surface.
- Different types of stainless steel: Different types of stainless steel respond differently to the PACD treatment. The respective process parameters must always be adapted to the specific alloy.
- Pre-treatment and post-treatment: Only experts can assess the impact of previously conducted pre-treatments on the PACD process, and the pre- and post-treatments which may be necessary to achieve the desired final result.
- Quality control: Stringent quality controls are essential for ensuring reproducible results and consistently high quality.
Our system
Chamber volume: 1.25 m3
Chamber dimensions: Diameter 800 mm, height 2,500 mm
Power supply: Voltage (100-1,000 V), current (10-300 A)
Temperature control: 300°C to 400°C
Data required for PACD treatment
To ensure the success of the PACD treatment, we require information from you about the characteristics of the workpieces to be treated and about the desired properties to be achieved. Our customer service will be happy to provide you with the relevant form. The information required includes the following:
- Material: Which stainless steel alloy (e.g. AISI 304, AISI 316) is to be treated?
- Dimensions and geometry: What is the size and shape of the workpiece, and how many workpieces are to be hardened?
- Surface condition: Have certain pre-treatments (e.g. cleaning, blasting) been performed, or are they desired?
- Required properties: What specifications are to be achieved? (degree of hardness, wear resistance, fatigue life, etc.)
- Special requirements: Are there additional requirements, such as selective hardening of specific areas?