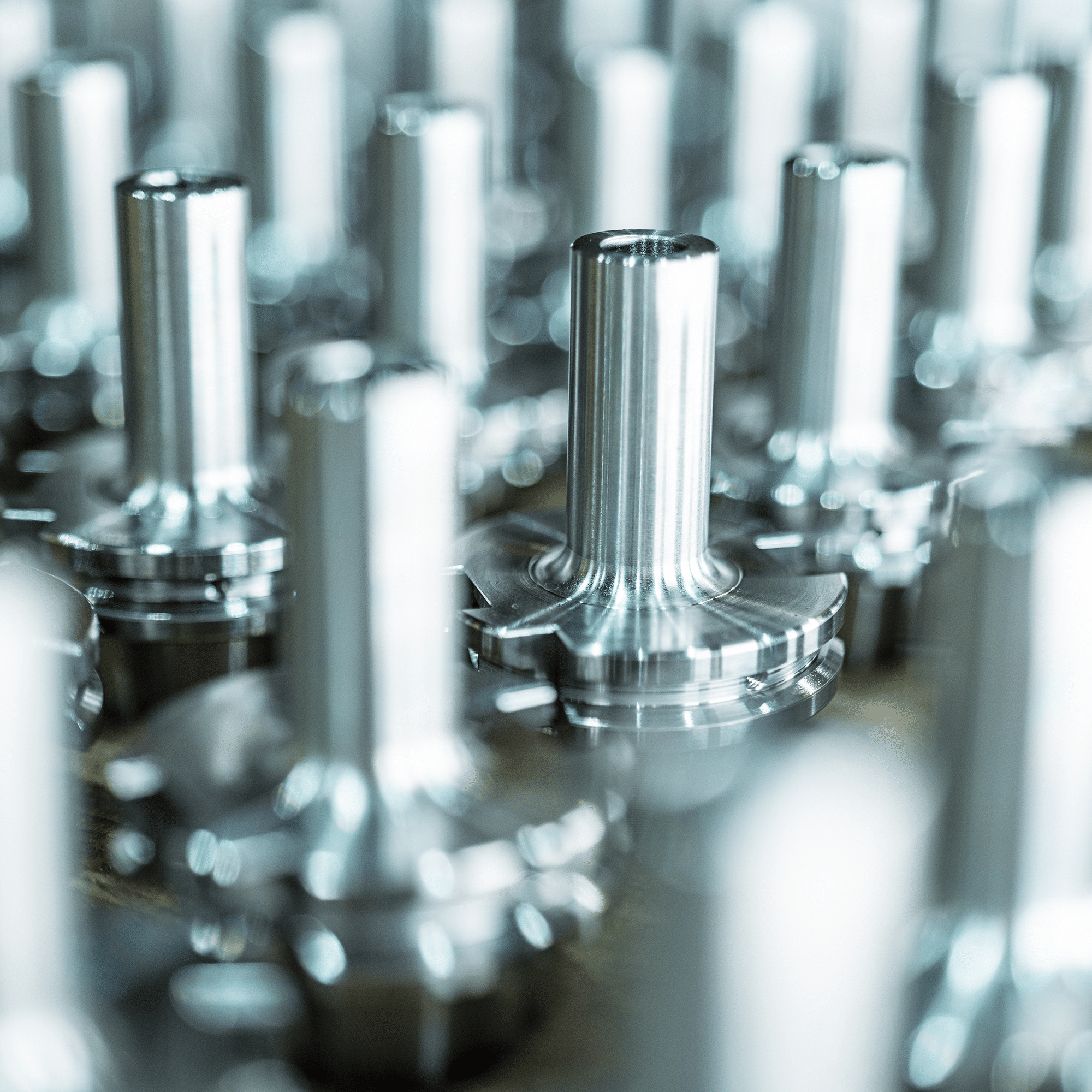
The process
Oxidising is a post-treatment which follows nitriding and applies an oxide layer to workpieces, thus creating a noticeable improvement in a wide variety of properties. The process is carried out by introducing oxygen at a temperature up to 570 °C.
Nitriding and nitrocarburising create a thin compound layer of only a few micrometres on the workpiece. During oxidising, the free iron molecules as well as the iron nitrides in this compound layer react with the introduced oxygen to produce stable iron oxide, which then accumulates as a thin oxide layer of no more than 3 µm on the surface of the component. This layer is extremely resistant to chemicals and, together with the compound layer, it gives the workpiece high corrosion resistance and other important properties.
If post-oxidation is planned, it forms the final step of the process, immediately after nitriding. The surface must not be processed further after oxidising, as this would remove the protective layer. The formation of a compound layer during nitriding is a prerequisite for successful, long-lasting oxidation. This is because the hardened compound layer consists mainly of iron nitride, while the underlying diffusion layer contains ferrite, to which the oxide layer adheres much less strongly.
Suitable materials
Since oxidising is a post-treatment of nitrided workpieces, all metals that can be nitrided are suitable for this process. In principle, these include all common cast and sintered materials, as well as non-alloy, low-alloy, and high-alloy steels.
Areas of application
Oxidising is a good alternative to burnishing, and can also be applied to materials that are not suitable for burnishing. Compared with burnishing, the protection against corrosion achieved by oxidising is considerably more effective. Studies have shown that it is comparable to the corrosion protection provided by a hard chrome coating with a thickness of 10 μm.
In addition to improving its mechanical properties, the process also enhances the component surface visually by giving it a colour that ranges between grey and black. The exact shade of the surface depends on the grade of the steel.
Oxidising is especially recommended for nitrided parts made of low-alloy materials where the requirements call for high resistance to wear and corrosion. These components include hydraulic cylinders, transmission spindles, and other moving and friction-loaded components.
The advantages at a glance
As a post-treatment, oxidising offers a wide range of advantages. Especially when combined with nitriding, these have a positive effect on the practical use of the components:
- high level of corrosion protection
- excellent resistance to wear
- improved operating characteristics
- enhanced sliding performance
- visual enhancement thanks to black colouring
Process locations
You will find Härtha in Germany, Italy, and the Netherlands. Refer to our interactive location overview to learn which other processes besides oxidising we offer at locations near you.