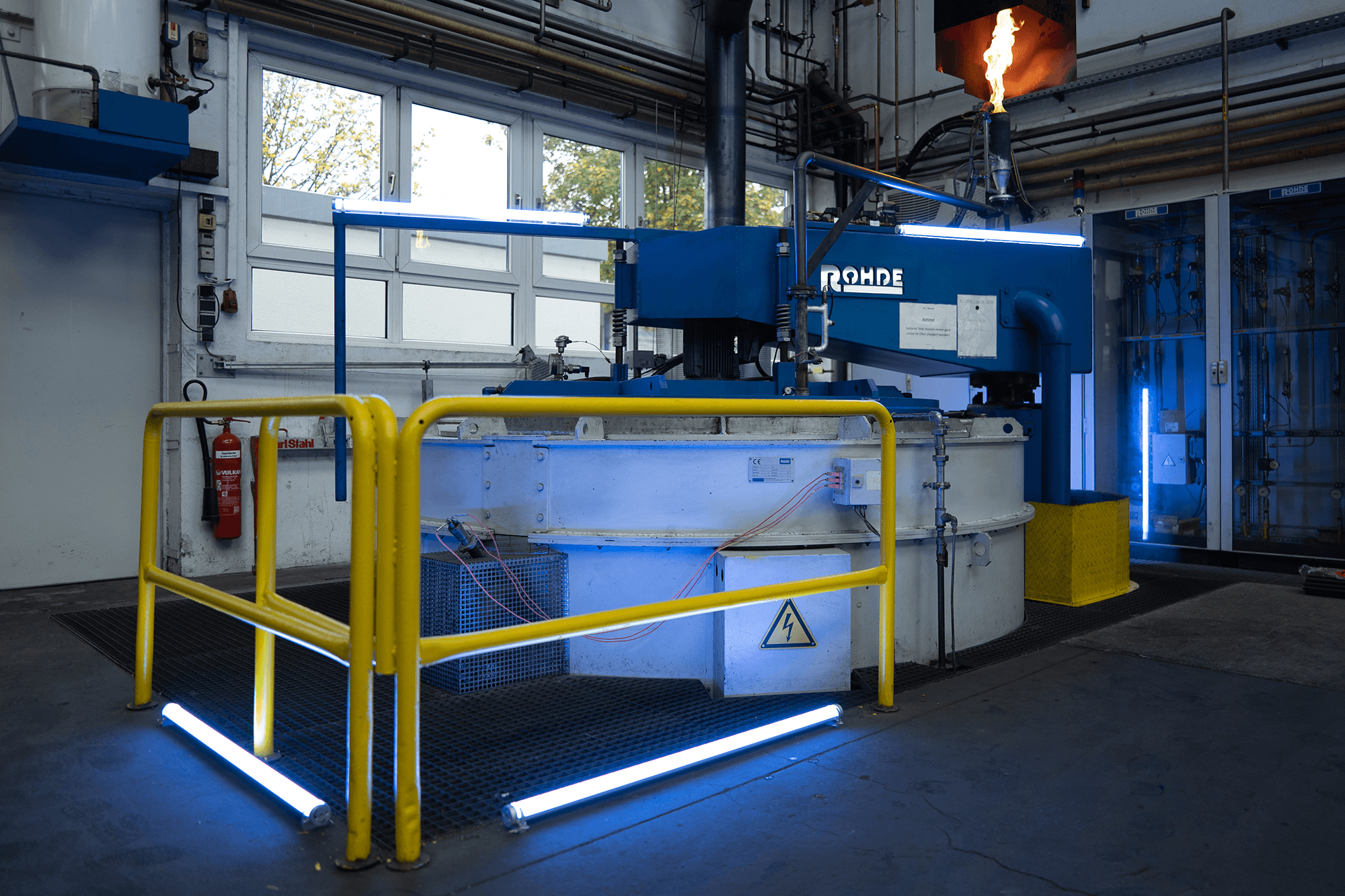
Subdivision of the annealing process
Annealing can be divided into three phases.
Phase 1: Heating
The first phase is the heating step. During this step, the workpiece is heated to the annealing temperature and then heated all the way through. In this phase, it is important to observe the specific heating rate for the respective material.
Phase 2: Dwell
The second phase is called the dwell phase. The component is held constant at the annealing temperature, allowing temperature equalisation throughout the entire workpiece. In addition, the desired physical and chemical processes can now be balanced. The necessary dwell time depends on the type of material, the shape of the component, and the position in the annealing furnace.
Phase 3: Cooling
The process concludes with the cooling. The component is now cooled down to the ambient temperature. The cooling rate can play an important role in this phase as well. This ends the annealing process.
Annealing colours for the annealing of steel
More complex thermal treatments
The three annealing phases may have to be subdivided further especially when high quality requirements are imposed on a material. For some types of material, the treatment is subdivided into nine stages. These subdivisions are specified in annealing specifications/annealing programmes. However, the term "annealing programme" is also used for several consecutive annealing processes applied to different products or to the same workpiece.
Distinction by annealing method
Annealing is categorised into the following methods:
- Normal annealing
- Soft annealing
- Annealing to spherical cementite
- stress-free annealing
- Coarse grain annealing
- Recrystallisation annealing
- Diffusion annealing or homogenisation annealing
- Low hydrogen annealing or hydrogen effusion annealing
The normalising of steels is also referred to as normal annealing. The goal of this process is to evenly distribute a fine-grained crystallite microstructure across the entire workpiece. The necessary temperature depends on the carbon content. Low-carbon metals can be treated by normal annealing up to 950 °C. Steels with a high carbon content, on the other hand, are normally annealed just below 800 °C.
The temperatures used during soft annealing range between 650 °C and 800 °C. In this temperature range, the precipitation of cementite and pearlite is reduced. The steel's hardness and strength are both reduced, and its formability is increased.
The process of ASC annealing, short for annealing on spherical cementite, is comparable to soft annealing. The focus here is on attaining a high degree of incorporated carbide, in order to enable cold forming at room temperature. This is achieved by cycle annealing and slow cooling.
The objective of stress-free annealing is to eliminate residual stress in the steel, without affecting its other properties. This is achieved at temperatures between 480
°C and 680 °C.
As the name suggests, coarse grain annealing increases the size of the crystallites, resulting in reduced strength and toughness - and creating ideal conditions for metal-cutting machining.
During recrystallisation annealing, the material is heated to a temperature just above the individual recrystallisation temperature. This temperature depends on the degree of deformation and the melting temperature of the material. It generally lies between 550 °C and 700 °C. The aim of this annealing method is to return crystallite microstructures previously altered by cold forming to their original state.
Another method is diffusion annealing, also called homogenisation annealing. At temperatures between 1,050 °C and 1,300 °C, foreign atoms are incorporated evenly into the metal lattice of the workpiece being treated. This process can take up to two days.
Finally, there is hydrogen effusion annealing, or low hydrogen annealing. At temperatures between 200 °C and 300 °C, an effusion process takes place. This involves the release of hydrogen atoms which previously embrittled the material.
The advantages at a glance
In summary, various annealing methods can yield the following benefits:
- Enhanced mechanical properties
- A microstructure better suited for cold forming
- Reduction of stresses
- Improved preparation for cutting and non-cutting machining
- Restoration of the initial state
Applications and materials
Annealing is a process that is generally suitable for all metals. However, it is primarily used for semi-finished products as well as for castings, cold-worked steels, and cold-worked wires.
Customer specifications for heat treatment (annealing)
Are you ready to commission annealing from us? Then we need the following information to make a proposal:
- The material designation
- The annealing method
- If applicable, the microstructural strength
- If applicable, the hardness in Brinell units (HB)
- The annealing microstructure
Process locations
Refer to our location overview to find out where we can process your annealing orders.